简介
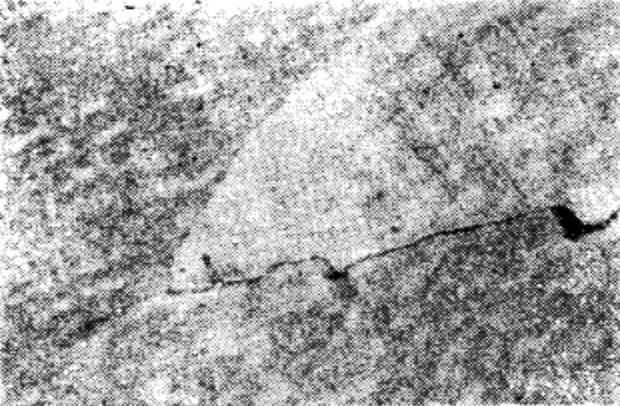
晶间裂纹
晶间裂纹是铸锭内部裂纹的一种特殊形式。它的主要特征是沿晶粒边界开裂。有些晶间裂纹比较细小,甚至需要借助放大镜才能辨认出来。发生晶间裂纹的根本原因,是在晶界附近存在着某些微量的低熔点物,并在晶粒之间存在着较大的应力。当在晶界上存在着某些低熔点物(或脆性物)时,晶粒之间的强度将大大减弱。
铸锭中心裂纹也大都是由晶间裂纹发展起来的。
避免发生晶间裂纹的主要措施,基本上与避免中心裂纹的措施是一致的,具体如下:
1.严格控制金属或合金的化学成分。例如,能够促进铸锭内裂的主成分应控制在中、下限;能够促进铸锭内裂的杂质越低越好;
2.采用分散供流的办法,以减低液穴深度;
3.降低铸造温度,或减慢铸造速度、减小冷却强度等。
但需指出的是,如对熔体进行变质处理,细化铸锭的结晶组织,对防止晶间裂纹有其特殊的意义。
晶间裂纹的形成
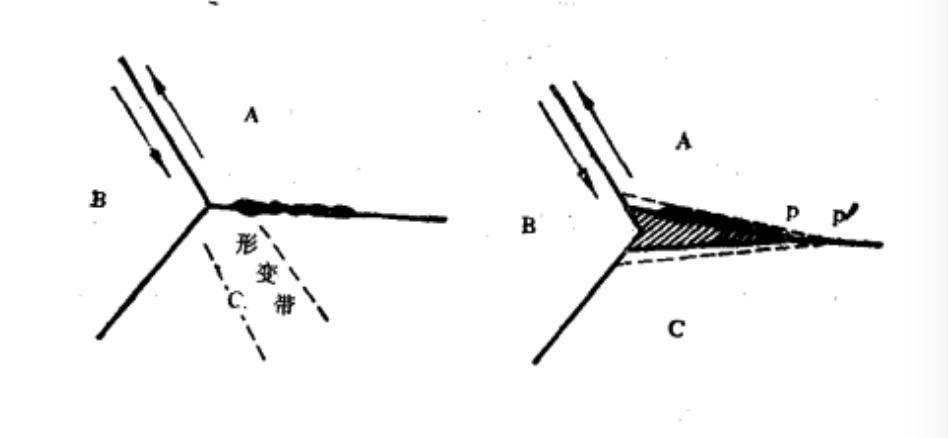
在高温,一定应力作用下晶间裂纹形成的示意图
让我们首先分析A、B、C三个晶粒交界处裂纹的形成。高温下的一定应力能使AB晶界产生相对滑移(如上图)。与此同时,在晶粒C如上图所示的形变带中将发生塑性变形,即位错在奥氏体的

滑移面上运动,以同AB晶界的相对滑移相配合。位错在运动过程中,或者由于形成割阶、位错缠结,或者由于遇到晶内第二相,或者由于遇到晶界,特别是晶界间隙相,使其运动受阻,塞积成列,如下图所示。领先位错运动受阻,后面的位错不能继续前进,塞积列中第i个位错距障碍物的距离与
成正比。因此塞积列中愈靠近障碍物的位错间距愈小。n条位错所构成的位错塞积列在晶界间隙相或晶内第二相障碍上所产生的力比外应力扩大n倍。于是C晶粒形变带中的塑性形变与AB晶界的相对滑移不相协调,在AC或BC晶界产生相当高的应力集中,一个尖劈形的晶问裂纹源得以形成(上图)。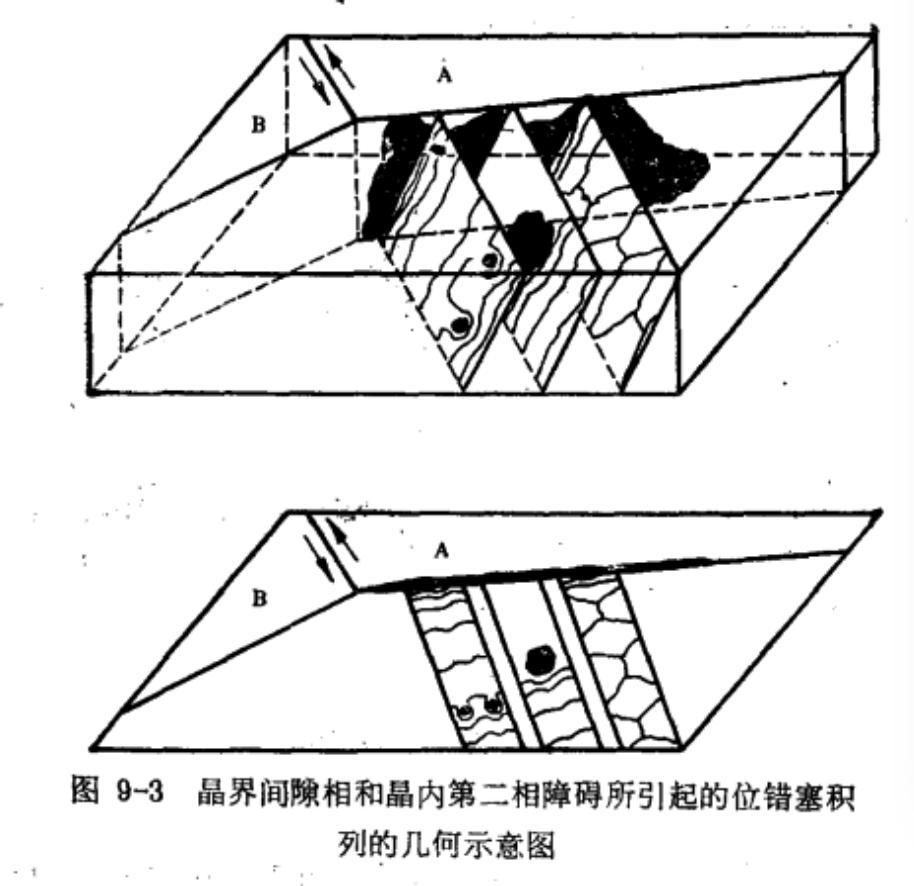
晶界间隙相和晶内第二相障碍所引起的位错塞积列的几何示意图
晶内过分强化,即位错运动过程中遇到难以逾越的障碍愈多,因而奥氏体中一般不发生解理断裂,上述晶间裂纹更容易形成。当晶界不存在相当多的大尺寸间隙相颗粒或薄片时,上述晶界滑移所产生的应力集中可能通过晶界迁移得到缓解,从而可以减缓合金中晶问裂纹的形成。低温高应力作用下,即使晶界强度较高,晶界滑移不易发生,但是对于晶内沉淀强化的实际合金,由于位错易于为沉淀粒子所塞积,应力集中的结果又不能使奥氏体发生解理断裂,因而容易形成晶间裂纹。晶界大尺寸间隙相,特别是大尺寸二维薄片状间隙相能促进晶间裂纹的形成。
类似于上述分析,断裂过程中。在不同的晶界滑移情况下,晶间裂纹的形成如图。
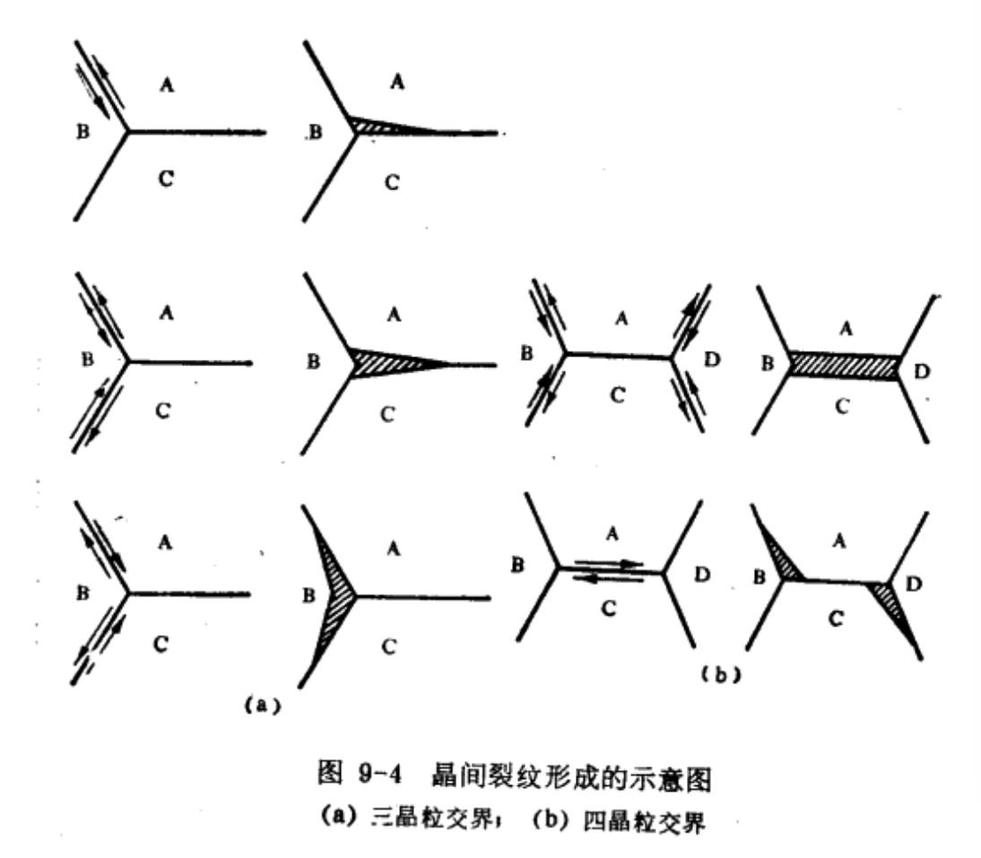
晶间裂纹形成的示意图
晶间裂纹的扩展与晶间断裂
由于外应力的不断作用,在裂纹前沿P产生应力集中。当晶间有相当数量的大尺寸二维薄片状间隙相或晶界相当平直时,裂纹将沿晶界向前扩展,其前沿由P达到

。然后,裂纹继续扩展,与其它晶间裂纹互相连通,最后导致瞬时晶间脆性断裂(下图a)。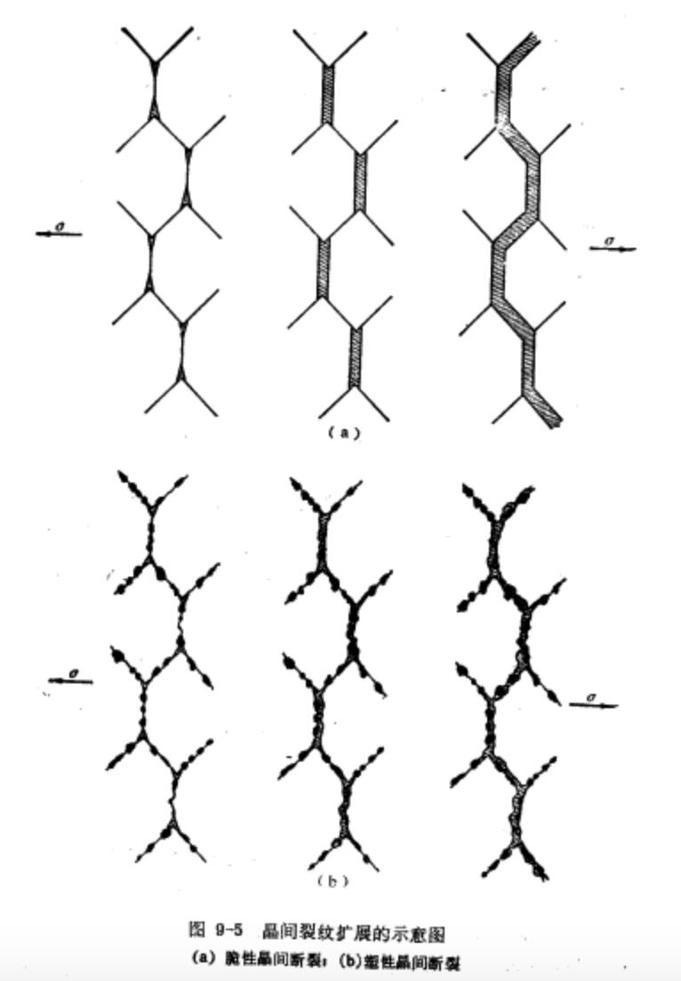
晶间裂纹扩展示意图
如果晶界上存在弥散分布的颗粒状间隙相或晶界弯折时,则在与应力垂直的横向晶界上,容易在颗粒状间隙相与母相界面或晶界弯折处产生空洞。高温下,特别是高温低速形变的条件下,裂纹的形成与扩展可能与扩散过程密切相关。合金中由于形变的发生,晶体缺陷,如空位,不断增多,这些空位为了减少其表面能,在外应力作用下,沿一定方向向晶界空洞聚集,使空洞逐渐长大,在晶界形成一串“空洞珠”。“空洞珠”互相结合而发展成具有波浪形截面的裂纹。这些裂纹继续扩展,与其它晶间裂纹互相连通,最后导致塑性晶间断裂(上图b)。如上所述,晶间脆性断裂或晶间塑性断裂主要包括四个过程:
1.裂纹的形核;
2.裂纹的迅速或缓慢扩展;
3.裂纹的互相连通;
4.瞬时断裂。
轴心晶间裂纹
特征1.横向低倍试片的轴心位置有沿晶粒间界裂开的一种形如蜘蛛网状的断续裂缝,严重时由轴心向外呈放射状裂开,产生在树枝状组织较严重的铬镍结构钢及铬镍不锈钢中,多出现在钢锭的中上部;
2.纵向断口呈宽窄不一的非结晶构造的较光滑的条带,有时有夹渣或夹杂颗粒;
3.在显微镜下看晶间裂纹处的夹杂物一般不严重,个别情况下夹杂物级别较高。
成因1.主要是钢锭在冷却和结晶过程中体积收缩,轴心区产生热应力和组织应力;
2.钢锭凝固时,因树枝状晶轴间化学成分不同,所以其临界转变点也不同,因发生相变有先有后,必然在钢锭内产生内应力,在较大内应力作用下,树枝晶与树枝晶之间形成晶间裂纹。当钢中气体含量较多时,晶间裂纹更容易发生和扩展。
判定及处理方法1.允许按盘、按段分别判定;
2.增大压缩比和压下率,可以使钢锭中心的晶间裂纹得到焊合。
减少方法1.高温脱模缓冷或红送初轧
这样做可以延缓锭心冷却速度和锭心结晶时两相共存时间以减少显微裂纹,以及减少整个钢锭随后冷却时的内应力。提高红送温度结果更明显,曾有资料介绍红送的6.2吨18

钢锭正常情况下蛛网裂分布在钢锭高度的70%~80%,宽度的15~30%区域内,对钢锭模进行保温,以提高热送温度之后,蛛网裂区缩小到钢锭高度的50%,宽度的6%。2.加大锻压比
典型的晶间裂纹中没有夹杂物,因此加大锻压比之后可能焊合。如18

钢以前采用退火或800℃左右红送始终存在级别0.5~1.0左右的蛛网裂,但改为轧锻成材并加大锻压比之后,消除了此缺陷。3.提高钢质
减少钢中气体和夹杂物对消除任何裂纹均有好处。在冶炼对气体较为敏感的高铬和铬镍钢种时尤其要注意。
但是在钢坯横向酸蚀试样轴心部位出现的蛛网状缺陷,并非全是轴心晶间裂纹。《钢的金相图谱-钢的宏观组织与缺陷》一书指出“由于非金属夹杂物被酸蚀掉或组织的不均匀性而形成的‘虚线’状轴心缺陷及沟状轴心缺陷不应当作轴心晶间裂缝”。