简介
可锻铸铁白口铸铁通过石墨化退火处理得到的一种高强韧铸铁。有较高的强度、塑性和冲击韧度,可以部分代替碳钢。它与灰口铸铁相比,可锻铸铁有较好的强度和塑性,特别是低温冲击性能较好,耐磨性和减振性优于普通碳素钢。这种铸铁因具有-定的塑性和韧性,所以俗称玛钢、马铁,又叫展性铸铁或韧性铸铁。黑心可锻铸铁用于冲击或震动和扭转载荷的零件,常用于制造汽车后桥、弹簧支架、低压阀门、管接头、工具扳手等。珠光体可锻铸铁常用来制造动力机械和农业机械的耐磨零件,国际上有用于制造汽车凸轮轴的例子。白心可锻铸铁由于可锻化退火时间长而较少应用(见铁素体可锻铸铁、珠光体可锻铸铁和白心可锻铸铁)。
生产过程
首先浇注成白口铸铁件,然后经可锻化退火(可锻化退火使渗碳体分解为团絮状石墨)而获得可锻铸铁件.
化学成分:
可锻铸铁的化学成分是: wC=2.2%~2.8%,wSi=1.0%~1.8%,wMn=0.3%~0.8%,wS≤0.2%,wP≤0.1%。
可锻铸铁的组织有二种类型:
铁素体(F)+团絮状石墨(G);
珠光体(P)+团絮状石墨(G)。
用途
可锻铸铁(malleable cast iron)汽车用金属材料。由一定化学成分的铁液浇铸成白口坯件,经过石墨化退火,石墨主要呈团絮状、絮状,有时呈少量团球状的铸铁。可锻铸铁与灰铸铁相比,具有较高的强度、韧性和冲击韧性。可锻铸铁根据化学成分、热处理工艺、性能以及组织不同分为黑心可锻铸铁、珠光体可锻铸铁以及白心可锻铸铁和球墨可锻铸铁四类。目前中国生产的可锻铸铁90%以上为黑心可锻铸铁。其他三类可锻铸铁应用较少。黑心可锻铸铁强度不高,但具有良好的塑性和韧性。可锻铸铁主要应用于汽车后桥桥壳、转向机构、低压阀、管接头等受冲击和震动的零件。
性能
白口铁的加工性能极差,但是经过高温回火后,有较高的强度和可塑性,可以切削加工。
由于可锻铸铁中的石墨呈团絮状,对基体的割裂作用较小,因此它的力学性能比灰铸铁高,塑性和韧性好,但可锻铸铁并不能进行锻压加工。可锻铸铁的基体组织不同,其性能也不一样,其中黑心可锻铸铁具有较高的塑性和韧性,而珠光体可锻铸铁具有较高的强度,硬度和耐磨性。
牌号及用途
牌号表示方法
可锻铸铁的牌号是由“KTH”(“可铁黑”三字汉语拼音字首)或“KTZ”(“可铁珠”三字汉语拼音字首)后附最低抗拉强度值(MPa)和最低断后伸长率的百分数表示。例如牌号KTH 350—10表示最低抗拉强度为350 MPa、最低断后伸长率为10%的黑心可锻铸铁,即铁素体可锻铸铁;KTZ 650—02表示最低抗拉强度为650 MPa、最低断后伸长率为2%的珠光体可锻铸铁。
常见的几种可锻铸铁
牌号、性能及用途(GB 9440—1988)
铸铁牌号KTH300—06、KTH330—08、KTH350—10、KTH370—12:用于制造管道配件、低压阀门、汽车拖拉机的后桥外壳、转向机构、机床零件等。
铸铁牌号KTZ450—06、KTZ550—04、KTZ650—02、KTZ700—02:制造强度要求较高、耐磨性较好的铸件,如齿轮箱、凸轮轴、曲轴、连杆、活塞环等
铸铁牌号KTB380—04、KTB380—12、KTB400—05、KTB450—07:此为白心可锻铸铁,仅限于制造薄壁铸件和焊接后不需进行热处理的铸件、由于工艺较复杂,故在机械制造上较少应用。
可锻铸铁的牌号表示方法
应用范围
黑心可锻铸铁的强度、硬度低,塑性、韧性好,用于载荷不大、承受较高冲击、振动的零件。
珠光体基体可锻铸铁因具有高的强度、硬度,用于载荷较高、耐磨损并有一定韧性要求的重要零件。
可锻铸铁的应用
如石油管道、炼油厂管道和商用及民用建筑的供气和供水系统的管件。
发展历史
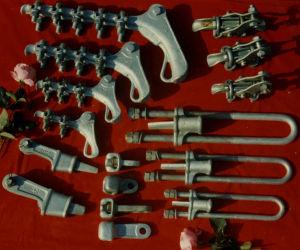
可锻铸铁
筒史中国是生产可锻铸铁历史最悠久的国家之一,早在战国初期就出现了用热处理方法使白口铸铁中与铁化合的碳成为石墨析出而获得了韧性铸铁的工艺。在河南洛阳出土的战国初期经退火表面脱碳的钢面白口铁锛,是当时已有退火操作的-例。在这基础上延长退火时间就可以生产韧性(可锻)铸铁。这-发明使铸铁在当时得以大量、广泛用于军事和农业生产。《孟子》记载了孟轲(约公元前390~305年)的话“许子以铁耕乎?”反映了公元前4世纪铸铁农具正在推广。公元1720~1722年,法国人雷奥米尔(Reaumur)发明了后来被通常称为“欧洲法”(Procede europeen)的白心可锻铸铁生产方法。1982年美国人塞斯博登(SethBoyden)通过偶然的热处理,把白口铸铁中的Fe3C进行了分解,使之析出团絮状石墨+金属基体(铁索体或珠光体)。他当时得到的可锻铸铁是铁素体基体的。这种方法通常称为“美国法”(黑心可锻铸铁)。种类
白心白心可锻铸铁,由法国人R.A.F. de罗茂于1722年研制成功。将碳、硅含量较低的白口铸铁密封在氧化介质中,在950~1050℃温度下保持几十个小时进行脱碳退火处理,就得到外层为铁素体、中心残留着少量珠光体和团絮状石墨的显微组织。其心部断口呈白色,故称为白心可锻铸铁。
黑心黑心可锻铸铁,由美国人S.博伊登于1826年在引进制造白心可锻铸铁工艺的基础上发展而成。将碳、硅含量较低的白口铸铁放在中性介质中进行石墨化处理后,在 850~950℃温度下保持几十小时,炉内冷却至720~740℃再保温十几小时,最后得到铁素体基体和团絮状石墨的铁素体黑心可锻铸铁;或在850~950℃下保温十几小时后出炉,空气中冷却,得到珠光体基体和团絮状石墨的珠光体黑心可锻铸铁。性能和用途可锻铸铁中石墨呈团絮状,含量较少,应力集中现象不太显著,对铸铁的有效负荷面积减小不多,抗拉强度可达300~700兆帕,延伸率可达2~12%,切削加工性能、抗氧化生长性能和耐蚀性能良好。可锻铸铁铸态组织为白口,铁水流动性较差,容易产生缩孔,热裂倾向较大,所以一般只适用于形状不太复杂的铸件。此外由于退火时间随壁厚加大而延长,同时过厚的铸件中心部分难达到完全退火,因此白心可锻铸铁件的壁厚一般不超过12毫米,黑心可锻铸铁壁厚不超过25毫米。铁素体可锻铸铁广泛用于汽车、拖拉机的轮圈、差速器壳和底盘零件,机床附件中的扳手,输电线路中的瓷瓶铁帽、线夹、碗头排板,纺织机械中的粗纺机和印花机盘头以及水油管道中的弯头、三通、接头、中压阀门等。珠光体可锻铸铁用于气阀摇杆、加煤机零件、高压接头阀体和汽车工业拨叉、差动齿轮箱等。白心可锻铸铁用于汽车零件吊架、驾驶盘柱叉肩、纺织机零件等。发展可锻铸铁的研究主要集中在铸态稳定碳化物,铸件中不出现游离石墨片,缩短退火时间以提高机械性能和使用性能等方面。此外,铸件厚度和重量限制范围有所扩大,现代已生产出壁厚2~80毫米或重达150千克的可锻铸铁件。
特点
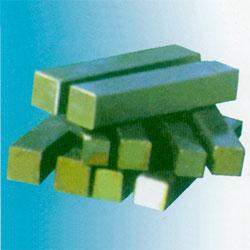
可锻铸铁
中国国家标准(GB9440-88)中的牌号基本符合国际标准(ISO5922-1981)。石墨化退火主要涉及固态石墨化机理、石墨化退火工艺的影响和各种元素对固态石墨化的影响。
(1)固态石墨化机理。白口生坯中的渗碳体是不稳定相,只要条件具备便可分解成稳定相--铁素体和石墨,这就是固态石墨化过程。必要条件是白口铸铁固态石墨化能否进行取决于渗碳体分解和石墨成长的热力学和动力学条件两个方面。热力学观点认为,渗碳体从低于铁-碳相图A,很多的温度条件下保温,亦可发生固态石墨化过程。但渗碳体的分解能否不断进行,石墨化过程能否最终完成,则在很大程度上取决于渗碳体分解后碳原子的扩散能力和可能性,使旧相消失,新相形成的各种阻力因素等动力学条件。在渗碳体及基体多相存在的情况下,石墨晶核最容易在渗碳体与周围固溶体的界面上产生;如果铸铁内有各种硫化物、氧化物等夹杂物微粒,则石墨晶核的形成就比较容易。要使白口铸铁中存在的石墨晶核继续长大,必须具备碳原子能强烈扩散的条件。纯铁碳合金较难于石墨化,有促进石墨化的元素存在时,能加速石墨化进程。关于铸铁固态石墨化机理许多观点,大多是根据传统的两阶段退火工艺提出的。高温阶段时,当加热到奥氏体温度区域,经过4个环节:在奥氏体-渗碳体界面上形核;渗碳体溶解于周围的奥氏体中;碳原子在奥氏体中由奥氏体渗碳体界面向奥氏体-石墨界面扩散;碳原子在石墨核心上沉淀导致石墨长大。在这阶段退火过程中,。渗碳体不断地溶解,石墨不断地长大,直至渗碳体全部溶解。此时铸铁的平衡组织为奥氏体加石墨。在低温阶段则发生转变成铁素体的共析转变,最后形成铁素体加石墨的平衡组织。由于采用低温石墨化退火工艺的问世,固态石墨化机理随之有所发展。加热温度不高于A,温度,而仅有720~750℃的保温阶段,铸铁组织由原来的珠光体加莱氏体直接转变为铁素体加石墨。关键是要改善较低温度下的石墨化动力条件,以及加强铸铁内在的石墨化因素。如细化渗碳体,细化晶粒增加界面,增加位错密度,从而增加初始石墨核心数以减少扩散距离。
(2)石墨化退火工艺的影响。第-阶段常用温度920~980℃保温,佚莱氏体中的共晶渗碳体不断溶入奥氏体而逐渐消失,团絮状石零逐渐形成。第二阶段常用温度710~730℃保温,或者由750℃缓慢(3~5℃/h)降温至700℃。预处理常用温度分高温预处理即在750℃左右保温1~2h,和低温预处理即在350~450℃保温3~5h。其作用在于增加石攫颗粒数,减小碳原子扩散距离,缩短退火周期,改善石墨形态。
(3)各种元素对固态石墨化的影响。碳能促进石翠化,增加退火的石墨核心数,缩短石最化时间,特别是缩短第二阶段石墨化的时间。硅强烈促进石墨化,能促进渗碳体的分解,故在允许限度以内提高铁液中的含硅量,能有力地缩短第-、第二阶段的退火时间。在炉前加硅铁或含硅的复合孕育剂可造成较大浓度起伏,有利于实现低温石墨化。锰能与硫生成MnS,故在适当含量范围内能缩短石墨化时间。但当自由锰量(锰与硫化合生成MnS以外的多余锰量)超过-定值(>0.15%~0.25%)或不足时(负值),则阻碍石墨化,尤其是阻碍第二阶段石墨化。硫强烈阻碍石墨化。当硫含量不很高时(<0.25%),可用锰中和其有害作用。当硫含量较高时,使石墨化退火困难。磷在凝固时微弱地促进石墨化,对退火过程中的固态石墨化影响不大。超过一定量时对第二阶段石墨化稍有阻碍作用。其他如铬、钼、钒、碲等均有强烈的阻碍石墨化作用;铝、锆、钙有较强促进石墨化作用。