简介
碳势又称碳位或碳的化学位。它是决定碳传递方向和限度的强度因素。碳势反映了碳从一个相转移到另外一个相的能力。
多相平衡时,每一种物质在互相平衡的各相中的化学位相等。根据这一原理,当钢在某种炉气中加热到平衡时,炉气的碳势(化学位μ )应与钢碳势(化学位μ )相等。因此,在恒温条件下,与一定成分的炉气相平衡的奥氏体的含碳量,表示了该状态下炉气的碳势。
炉气碳势可采用一简单方法测量:将厚度小于0.1 mm的低碳钢箔置于渗碳炉中,经过穿透渗碳后测定其含碳量,即代表炉气的“碳势”。
炉气的碳势是炉气渗碳能力的表征,与炉气成分及温度有关,它的高低反映了炉气渗碳能力的强弱。炉气碳势控制是气体渗碳的关键控制参数,碳势控制精度决定了工件表面含碳量的精度。碳势受很多因素的影响,诸如CO、HO、O、CH、CO、H分压、炉温、炉内总压力、加热炉的类型、原料气的种类等。
碳势控制原理
传统的渗碳炉控制系统均比较简单,主要有控制温度和碳势两个参数。渗碳过程往往不在控制之列,而且,温度控制大都采用模拟仪表控制,控温精度较低,一般为±5~±10℃。碳势控制一般采用手动控制,比如通过控制煤油滴数,进而定性控制碳势。显然,在这种控制系统下进行渗碳,气氛成分波动很大,渗碳质量很难得到保证,采用上述方法控制碳势效果欠佳。
(1)渗碳控制系统结构
由计算机控制的渗碳系统可以分为输入系统、计算机系统和输出控制系统。
①输入系统。该系统可以完成温度信号和碳势信号的采集并放大。温度信号由热电偶采集,碳势信号则由电阻探头采集,它们在进入通道放大器后,均转化为电压信号。
②计算机系统。由通道放大器输出的温度信号和碳势信号,先经过A/D转换,然后进入计算机。计算机通过执行采样模块、显示模块及打印模块,可以经数码管显示装置和打印机实时地显示和打印工艺参数,如温度、碳势、时间等。计算机运行控制模块后,可以分别计算出温度和碳势控制量,并经PIO口输出控制量。
③输出控制系统。计算机输出信号首先进入光电隔离电路,然后才分别输送至有关的控制系统。输出控制系统包括报警与指示系统、温度控制系统和碳势控制系统。
报警系统可以完成渗碳炉的超温报警、碳势超限报警、工艺到时报警、热电偶断偶报警以及电阻探头断丝报警等。报警以灯光和声音同时显现。报警类别不同,灯光闪烁情况将不同,声音类别亦不同。用户可以根据声光报警的情况,方便地判断报警原因,并及时地予以处理。指示系统主要用来指示渗碳炉工作状态。该系统可以设置指示灯,以分别指示炉子通电情况、步进电机的旋转、电磁阀的开启以及柱塞泵的行程等状态。温度控制系统和碳势控制系统,则分别用来完成炉温和炉气碳势的控制。在输出控制系统中,这两部分是关键。
(2)温度控制系统
当计算机发出高电平或一定电压信号时,输出信号,触发可控硅使其导通,炉子通电。固态继电器输入回路接通,固态继电器便有反之,当计算机发出低电平或0V电压信号时,固态继电器输入回路不通,无电流,则亦无输出,可控硅不导通,炉子断电。可见,经过该触发电路,计算机便可以根据炉温情况,控制炉子通电情况,进而精确控制炉温。
在温控电路中,主要元件为固态继电器,固态继电器是由集成元件组装成的无触点开关。固态继电器内部电路复杂,由于其具有很高的集成度及隔离措施,因此具有很强的抗干扰能力。使用性能稳定。所以,采用固态继电器实现可控硅过零触发,触发效果很好,控温精度可达±1℃。另外,该触发电路还具有原理简单、接线容易等特点。
(3)碳势控制系统
现以甲醇、煤油和水作为渗碳介质举例说明渗碳系统工作过程。上述渗碳介质中甲醇为载体气,煤油为富化气,水为稀释剂。渗碳时,甲醇以一定速度滴入炉内,其滴量是固定的。炉气碳势便通过调节煤油滴量而控制。煤油由柱塞泵打入炉内,煤油滴量由柱塞泵行程控制,而柱塞泵的行程又是由步进电机控制的。步进电机可以正转,也可以反转,即可以按照要求增大或减小柱塞泵的行程。这种方法,可以实现煤油的连续滴入,是连续式控制的方法。若炉气碳势超限,可打开供水阀,使水滴入炉内,以迅速降低炉内碳势。从这个工作过程可以看出,碳势控制系统应该包含甲醇阀控制电路、供水阀控制电路、柱塞泵启动电路及其步进电机控制电路。
碳势控制
可将炉内气氛气体的碳势定义为:在特定温度下与钢的碳含量平衡的气氛气体的碳含量。例如,要在1121℃下烧结由铁一石墨混合粉压制的压坯和制成的烧结钢的碳含量为0.8%,则炉内气氛气体的碳势于烧结温度1121℃下必须为0.8%C。
传统的碳势控制,原则上都是采用控制水蒸气含量(露点)或CO含量或氧含量的方法。
控制的原理可用下列平衡反应来说明:
2CO═C+CO
上式的平衡常数K为:K=αP/P
式中α是碳的活度,P和P分别为CO与CO的分压,该式变形可得出下式:
α=K/P /P
α的值与碳势有关。式中的K只取决于温度,而P基本上保持为常数,因此,碳势可通过改变CO而得到控制。所以,控制气氛气体的CO含量可作为控制碳势的一种方法。
通过控制水蒸气压力控制碳势的原理,可用上式来说明。在平衡状态下,HO的分压与CO的分压有关。
碳势图
通常使用碳作为还原剂来判断各种金属氧化物的还原难易程度。碳与金属氧化物MO的反应式如下:
C + 1/yMO—→x/yM + CO △G =A+BT
在高温条件下,CO为气体,碳为固态,而MO和M则有可能发生相变(如金属铝的熔点仅为933K)。利用热力学数据可计算出碳还原各种金属氧化物的标准吉布斯自由能变化与温度的关系,即碳势图(见下图)。
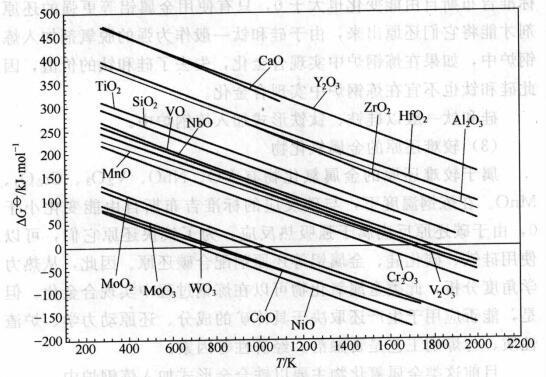
碳势图
影响因素
影响钢脱碳的因素有钢料的化学成分,加热温度,保温时间和煤气成分等。
1.钢料的化学成分对脱碳的影响
钢料的化学成分对脱碳有很大影响。钢中含碳量愈高脱碳倾向愈大W、Al、Si、Co等元素都使钢脱碳倾向增加;而 Cr、Mn等元素能阻止钢脱碳。
2.加热温度的影响
随着加热温度的提高,脱碳层的深度不断增加。一般低于1000℃时,钢表面的氧化皮阻碍碳的扩散,脱碳比氧化慢,但随着温度升高,一方面氧化皮形成速度增加;另一方面氧化皮下碳的扩散速度也加快,此时氧化皮失去保护能力,达到某一温度后脱碳反而比氧化快。
3.保温时间和加热次数的影响
加热时间越长,加热火次愈多,脱碳层愈深,但脱碳层并不与时间成正比增加。例如高速钢的脱碳层在1000℃加热0.5h,深度达0.4mm;加热4h达1.0mm;加热12h后达1.2mm。
4.炉内气氛对脱碳的影响
在加热过程中,由于燃料成分,燃烧条件及温度不同,使燃烧产物中含有不同的气体,因而构成不同的炉内气氛,有氧化性的也有还原性的。他们对钢的作用是不同的。氧化性气氛引起钢的氧化与脱碳,其中脱碳能力最强的介质是HO(汽),其次是CO与O,最后是H;而有些气氛则使钢增碳,如 CO和 CH。炉内空气过剩系数α大小对脱碳也有重要的影响:当α过小时、燃烧产物中出现H,在潮湿的氢气内的脱碳速度随着含水量的增加而增大。因此,在煤气无氧化加热炉中加热,当炉气中含HO较多时,也要引起脱碳;当α过大时,由于形成的氧化皮多,阻碍着碳的扩散,故可减小脱碳层的深度。在中性介质中加热时,可使脱碳最少。