历史背景
以前单位自制冰棒的人一定记得,那种冰棒非常非常硬,一点不象如今的冰棒这么松软,这是为什么呢?
这里就要先说说合金的“热脆”现象了。“热脆”是指合金在加热到远没达到该成分合金的理论熔点的情况下,出现的一敲就散架的现象,看起来好像是太脆,太酥了,所以被称为“热脆”。它出现的原因是因为,当合金在正常冷却速度的情况下,并不是象纯种金属那样开始凝固和结束凝固的温度是相同的(即有熔点),而是有一个范围的,而且先凝固的合金成分和后凝固的不同。先凝固的成分具有更高的熔点,化学成分和没凝固的也不相同,先凝固的部分占用掉的金属成分会改变剩余未凝固金属的化学成分,使它的完全凝固温度比之前更低,越来越低。当最后凝固之后,整块合金中的成分并不是处处相同的,而是先凝固的部分和后凝固的部分具有不同的成分比,所以具有不同的熔化温度。而我们通常说合金的成分比是指它们的总的成分比,这样我们根据总的成分比判断的熔化温度就和实际合金当中存在的最低熔化温度不符合,有时要高很多。当我们自以为还远没达到合金的熔化温度时,合金当中实际上已经有部分金属熔化了,而且因为冷却是自表向里的关系,这些易熔成分都是处于垂直合金表面呈放射状向里密密麻麻分布高熔点成分的针状体的间隙中的,所以这样的合金就一敲就碎,显得非常没有强度了。
冰棒
水中如果加入了很多溶解物比如糖,就相当于是合金,它在结冰的时候也会出现合金的类似现象,糖越多,这种现象越明显。冰棒之所以松软就是因为其中放的糖多,结冰的时候,先结冰的是熔点高的几乎不含糖的水,温度逐渐降低,结冰的也逐渐是含糖量高的水,因为制冰棒的温度不会特别低,所以甚至可能有部分很甜的糖水,最后根本都没结冰,即使结冰了,因为它们的熔点非常低,一拿出来吃的时候就先熔化了,所以,这样的冰棒吃起来就象刨冰似的,非常松软。而含糖量低的冰棒(放糖精,只要一点点就很甜),几乎都是在0度结冰的,拿出来吃的时候,要熔化也是从外往里熔化,里面的始终是一块整体,不会出现先熔化的间隙,所以非常硬。
根据上面的知识我们还可以理解下面这些:
松软的冰棒,外面的部分没有里面甜,先熔化的部分更甜(我吃冰棒总是使劲的把冰棒的甜水吸干,剩下的部分就是几乎没甜味的冰了,相信很多人都有这种体验),松软的冰棒会有由外向里刺的针状的冰晶,里面是最后凝固的最甜的部分。
硬的冰棒没有上面这些特性,就是一砣死冰,里里外外一样甜,不存在先熔化的更甜的水,也没有空隙让你去吸,你只能从外到里把它熔化掉。
板坯的热脆性与淬火处理
传统的板材生产,连铸板坯在坯库存放冷却后,再装人加热炉进行加热、轧制,对冷坯加热的时间长、效率低、能耗高。近年来,许多生产厂实现直接热装工艺,以节约能源,提高生产效率。然而,直接热装工艺不象传统冷装工艺那样可以防止或减轻某些化合物析出对轧制过程的影响,在轧制某些热装钢种时,会在板材表面产生裂纹,这就是热脆性问题。
热脆性产生机理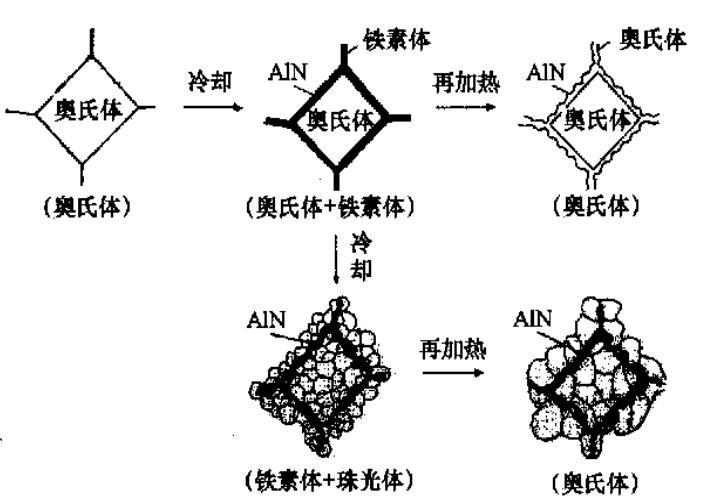
图1 不同加热过程AIN的析出情况
研究表明,氮化铝[AIN]的析出是直接热装工艺中热脆性问题 产生的根源,在多数铝镇静钢中都有氮化铝存在。铸坯在经历从奥氏体到奥氏体+铁素体的相变过程中,氮化铝在奥氏体晶界析出,如果此时将板坯装入加热炉加热,即使板坯又经过另一相变(由奥氏体+铁素体变为奥氏体),但析出物仍然在奥氏体晶界上,见图1。析出物成为降低晶粒间结合力的薄弱点,晶粒的可迁移性减弱,导致微观结构中晶粒边界强度降低。在轧制过程中板坯表面在晶界处撕裂,产生表面裂纹。这种裂纹的形状类似于横向裂纹或网状裂纹,当有其它应力增加因素存在和/或因板坯表面不规则(如振痕等)产生应力集中时,结果将会更严重。氮化铝的析出也恶化了与其它析出物和或残余元素相关联的问题,铜、钒、铌等元素本身会导致有裂纹倾向的微观结构的产生。如果这些元素析出产生的微观结构的弱化与曲于氮化铝析出造成的结构弱化相叠加,铸坯直接热装轧制将会出现严重的热脆性问题。
热脆性的解决办法及比较(1)加入合金法
通常加入钛固定氮,避免氮化铝的形成。这种办法是有效的,但会增加生产成本。
(2)高温铸坯热装法
采用提高拉速、降低冷却强度等措施,使铸坯一直保持高温,即铸坯不经历从奥氏体到奥氏体+铁素体的相变过程,防止氮化铝的析出。
(3)铸坯冷装法
采用传统的冷装工艺,铸坯经历了从奥氏体到奥氏体+铁索体的相变过程且有氮化铝的析出。但如图1所示,随着在坯库的继续冷却,铸坯又经历了从奥氏体+铁素体到铁素体+珠光体的相变过程。这个相变导致了钢的再结晶,再结晶把析出物包围在新形成的晶粒内,析出物不在晶界上,晶问强度增加,此时再将铸坯装入加热炉加热轧制,就不会出现热脆性问题。但这种工艺显然不能达到热装的效果。
(4)钢水成分控制法
钢水中[N]和[A1]含量达到一定值时,才会有氮化铝的形成及析出,如果控制钢水中[N]和[A1]含量,就会避免或减少氮化铝的形成及析出,从而避免热脆性问题。传统的解决热脆性问题的办法都有一定的局限性及缺点。最近国外开发了一种新的解决方案,即铸坯淬火处理,它既能解决热脆性问题,又能实现铸坯的直接热装。
淬火处理淬火处理是对出导向段的铸坯喷水强制冷却,使铸坯表面温度急剧冷却至某一特定温度的处理措蓝,经处理后的铸.坯可以热装。
(1)淬火处理原理
实践表明,析出只发生在凝固铸坯的表层,因此只需将该部分铸坯淬火,使其快速冷却,经历再结晶过程,就像在坯库自然冷却时那样,而铸坯心部仍然保持高温。尽管淬火后产生了非常细的马氏体,但在装入加热炉之前,高温心部对马氏体有退火作用。
(2)淬火处理设备及工艺
淬火处理设备是置于辊道上的一种箱形设备,内部布置若干排喷嘴,可单独控制或按组进行控制。当铸坯从箱内经过时,喷嘴对铸坯表面喷水,使铸坯表层快速冷却,完成淬火处理。铸坯淬火处理一般在出铸坯导向段后进切割之前进行,有些厂家在切割后进行。淬火处理后铸坯表面温度及淬透深度至关重要,这影响到淬火处理的效果。影响铸坯表面温度的因素有钢种、铸坯断面尺寸、进淬火箱前铸坯温度及冷却强度,其中以冷却强度最为重要。根据钢种、铸坯断面尺寸、进淬火箱前铸坯温度及通过淬火箱的速度等参数计算喷水压力及流量,并实现动态配水。有些厂家把淬火配水与二冷配水结合在一起考虑,在计算机动态配水模型中一并计算淬火配水量。淬火处理后铸坯表面温度一般在

,淬透深度为10mm左右。(3)淬火处理的优点
①提高产品质量,防止由热脆产生的裂纹;
②淬火处理可以给生产工艺带来灵活性,即对钢水中[N]和[A1]的含量要求可以适当放宽;
③能实现某些钢种铸坯的直接热装,提高热装比,节省能源,提高生产率与冷装相比可降低燃料消耗40%;
④采用淬火处理可以减少坯库面积。
(4)淬火处理的局限
①碳含量

的钢以及含矾[V]的钢不能进行淬火处理。因为这些钢进行淬火处理时,会使铸坯产生其它缺陷。这类钢只有通过传统的生产工艺,即下线到坯库,自然冷却到环境温度再冷装进入加热炉。②钢中氢只有铸坯在坯库里缓慢冷却才能逸出,如果对此类铸坯进行淬火处理,然后热装,则铸坯中氢不能逸出,在轧制过程中会造成新的缺陷,影响产品质量。
研究结论(1)与其它解决板坯热脆性的办法相比,淬火处理具有灵活性,既可避免热脆性,叉能实现热装;
(2)淬火处理也有其局限性,在某些情况下不能采用。