分类
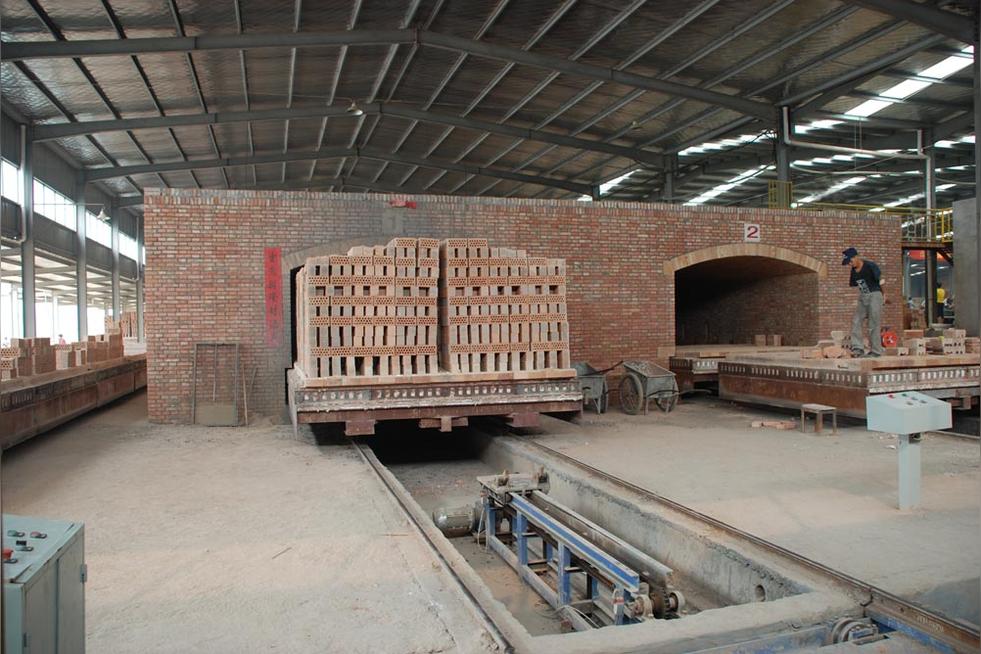
隧道窑
隧道窑有各种不同的分类方法,大致归纳为:1.按照烧成温度的高低可分为:
(1)低温隧道窑(1000~1350℃);
(2)中温隧道窑(1350~1550℃);
(3)高温隧道窑(1550~1750℃);
(4)超高温隧道窑(1750~1950℃)。
2.按照烧成品种可分为:
(1)耐火材料隧道窑;
(2)陶瓷隧道窑;
(3)红砖隧道窑。
3.按热源可分为:
(1)火焰隧道窑;
(2)电热隧道窑。
4.按火焰是否进入隧道可分为:
(1)明焰隧道窑;
(2)隔焰隧道窑;
(3)半隔焰隧道窑。
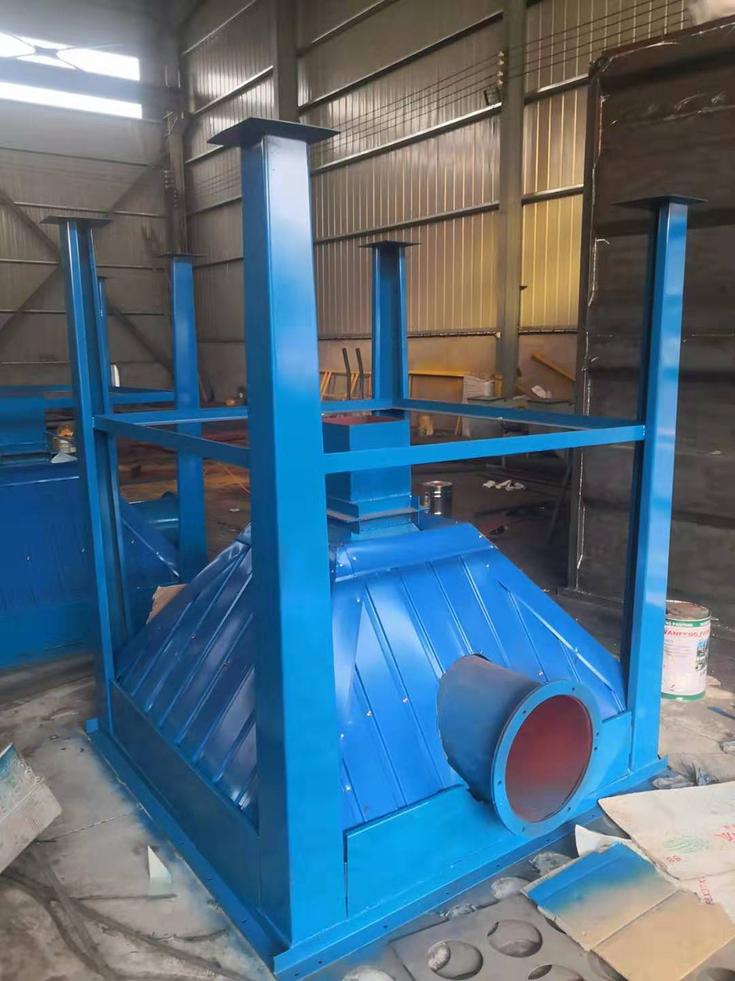
隧道窑
5.按窑内运输设备可分为:(1)车式隧道窑;
(2)推板隧道窑;
(3)辊底隧道窑;
(4)输送带隧道窑;
(5)步进式隧道窑;
(6)气垫式隧道窑。
6.按通道多少可分为:
(1)单通道隧道窑;
(2)多通道隧道窑。
结构
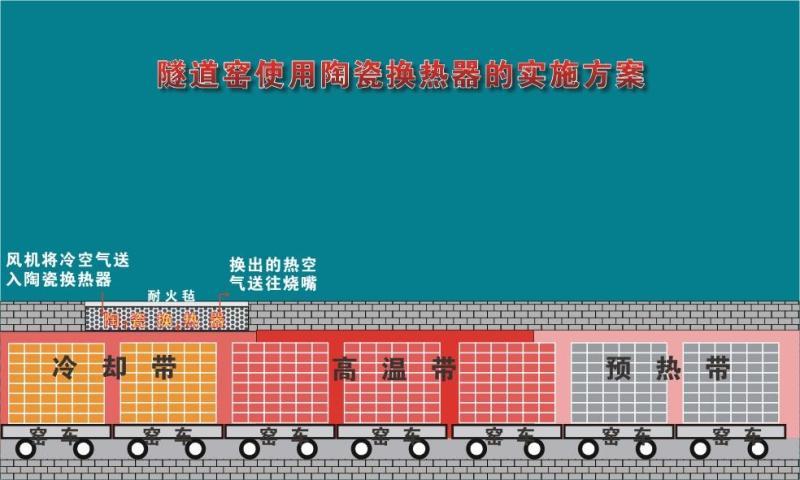
隧道窑
隧道窑主要包括以下几种:窑体、窑内输送设备、燃料燃烧系统、通风设备。窑体:隧道窑系统的主要部分,窑体上设有各种气流进出口。
窑内输送设备:窑车与窑具。
燃料燃烧系统:包括燃料输送管道、燃料预热、燃烧器等。隧道窑的加热燃烧主要是重油,轻柴油,和天然气煤气,原有的直燃煤方式已不多用。油类燃烧配备有储油罐和燃烧喷嘴。因油类成本较高使用较多的仍是天然气和煤气,天然气是通过天然气管道将天然气输送至窑炉有专门的天然气烧嘴进行喷射燃烧。煤气燃烧除了有专一的煤气管道输送至炉窑外,隧道窑用户大都自备有煤气发生炉进行煤气的生产,由煤气发生炉所产的煤气经过管道输送至隧道窑燃烧室,通过煤气烧嘴进行喷射燃烧。
通风设备:包括排烟系统、气幕搅动系统和冷却系统。其作用是使得窑内气流按一定方向流动。
工作原理
隧道窑始于1765年,当时只能烧陶瓷的釉上彩,到了1810年,有可以用来烧砖或陶器的,从1906年起,才用来烧瓷胎。最初著名的隧道窑,是福基伦式,到了1910年以后,就渐渐有了许多改进的方式。
隧道窑一般是一条长的直线形隧道,其两侧及顶部有固定的墙壁及拱顶,底部铺设的轨道上运行着窑车。燃烧设备设在隧道窑的中部两侧,构成了固定的高温带--烧成带,燃烧产生的高温烟气在隧道窑前端烟囱或引风机的作用下,沿着隧道向窑头方向流动,同时逐步地预热进入窑内的制品,这一段构成了隧道窑的预热带。在隧道窑的窑尾鼓入冷风,冷却隧道窑内后一段的制品,鼓入的冷风流经制品而被加热后,再抽出送入干燥器作为干燥生坯的热源,这一段便构成了隧道窑的冷却带。
在台车上放置装入陶瓷制品的匣钵,连续地由预热带的入口慢慢地推入(常用机械推入),而载有烧成品的台车,就由冷却带的出口渐次被推出来(约1小时左右,推出一车)。
应用于钢坯连续加热,或陶瓷连续烧结。
工作过程
粘土质陶瓷的烧成过程发生的物理化学变化:共有以下九个阶段。
1)20~200℃,排除残余水。
入窑水分要求:<1%,快烧<0.5%;升温速度:20~35℃/h
2)200~500℃,排除结构水。
指粘土矿物中的结晶水和层间水,安全阶段,可快烧,40~50℃/hr。
3)500~700℃,石英晶型转化。
573℃时由β-SiO2转变成α-SiO2,体积膨胀,易变形开裂,升温应慢,升温速度:20~30℃/hr。
4)700~1050℃,氧化阶段。
进行氧化反应和分解反应。硫化铁、有机物氧化,碳酸盐、硫酸盐、氢氧化铁分解,放出SO2和CO2及水蒸气等气体,应在釉面封闭以前氧清氧透,保证良好的氧化气氛和充分的氧化时间,减少窑内温差,适当进行中火保温,否则易出现质量缺陷,如黑点、青边,发黄、起泡等。气氛要求:O2=4~5%,CO<1%
5)1050~1200℃,还原阶段。
使氧化铁还原为氧化亚铁,褐黄变为青色,改善制品色泽,达到白里泛青,即“白如玉”的效果。
要求:升温慢,使气体充分排除,减少坯泡;保证气氛,避免重新氧化,CO=2~4%;保证时间,以利于还原反应进行彻底。
6)1200℃~烧成温度,烧结阶段。
坯体中出现玻璃相,气、固、液相扩散而达致密化,该传质过程与坯体的厚度平方成反比,故烧成时间与坯体厚度平方成正比。应据此确定高火保温时间(1~2小时),进行高火保温。
要求:升温速度10~30℃/hr,CO=1%,
7)烧成温度~700℃,急冷阶段。
产品处于热塑性阶段,可直接吹冷风急冷,冷却速度达120℃/hr
8)700~400℃,缓冷阶段。
石英晶型转化,体积收缩,而液相刚凝结,较脆弱,易惊釉、开裂,降温速度:<80~90℃/hr。
9)400~80℃,快冷阶段。
此时制品强度大,可直接鼓冷风快速冷却。
分带
隧道窑可分为预热带、烧成带、冷却带。
1、预热带占窑总长的30-45%,温度范围是室温~900℃;车上坯体与来自烧成带燃料燃烧产生的烟气接触,逐渐被加热,完成坯体的预热过程。
2、烧成带占窑总长的10-33%,温度范围是900℃~最高温度;坯体借助燃料燃烧所释放出的热量,达到所要求的最高烧成温度,完成坯体的烧成过程。
3、冷却带占窑总长的38-46%,温度范围是最高温度~制品出窑温度;高温烧成的制品进入冷却带,与从窑尾鼓入的大量冷空气进行热交换,完成坯体的冷却过程。
特点
优点隧道窑与间歇式的旧式倒焰窑相比较,具有一系列的优点。
1、生产连续化,周期短,产量大,质量高。
2、利用逆流原理工作,因此热利用率高,燃料经济,因为热量的保持和余热的利用都很良好,所以燃料很节省,较倒焰窑可以节省燃料50-60%左右。
3、烧成时间减短,比较普通大窑由装窑到出空需要3-5天,而隧道窑约有20小时左右就可以完成。
4、节省劳力。不但烧成时操作简便,而且装窑和出窑的操作都在窑外进行,也很便利,改善了操作人员的劳动条件,减轻了劳动强度。
5、提高质量。预热带、烧成带、冷却带三部分的温度,常常保持一定的范围,容易掌握其烧成规律,因此质量也较好,破损率也少。
6、窑和窑具都耐久。因为窑内不受急冷急热的影响,所以窑体使用寿命长,一般5-7年才修理一次。
但是,隧道窑建造所需材料和设备较多,因此一次投资较大。因是连续烧成窑,所以烧成制度不宜随
意变动,一般只适用大批量的生产和对烧成制度要求基本相同的制品,灵活性较差。
缺点1、其隧道窑建造所需材料和设备较多,因此一次投资较大;
2、对于不同制品必须全面改变焙烧工艺制度;生产技术要求严格;窑车易损坏,维修工作量大等。
节能方式
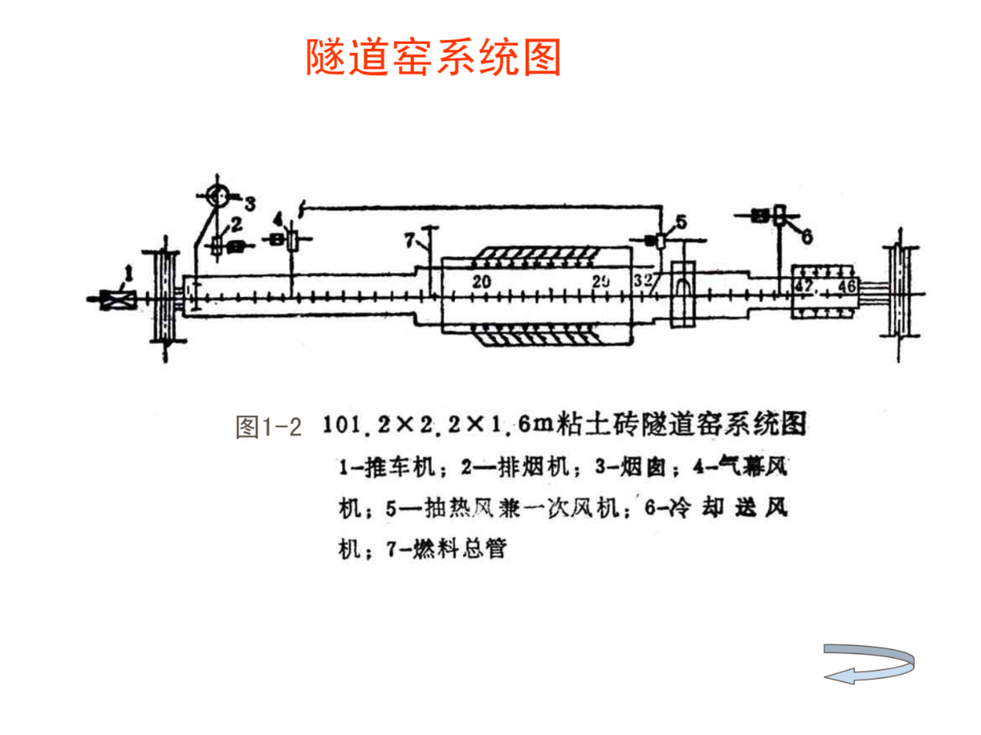
隧道窑
由于隧道窑是连续性窑炉,热利用较好,且多数隧道窑使用的助燃空气采取的是自然风或在冷却带吹入冷风,从而使空气变热。虽然余热利用,但因为抽出的热空气中,混入有非常多高温带燃烧过的废气,所以导致助燃空气中氧气不足,燃烧效果不佳。使用换热器换出来的热空气是新鲜的热空气,可达到最佳的助燃效果。如果使用金属换热器,可以进行一部分的余热回收,但如果冷却带温度达到800度以上,金属换热器非常容易被高温损坏。操作方法
第一、改变坯垛的码放形式,在中、下部加头,减少孔道,降低炕腿高度。这一措施尤其是适用于没有随着季节变化而改动码窑方法的情况,对于冬季仍使用夏季高炕腿的厂家,特别适用。
第二、降低近闸的使用高度,让保温带底部降温速度慢一些。
第三、适当延长保温带,延长供风的距离和时间。
第四、如因冷风进入量过大,使保温带冷却降温过快时,可减少冷风进入量,降低保温带的冷却降温速度。
第五、少量勤添,重烧后火。或者通过火眼在保温带第一排前添人炉灰“堵后风”。