基本类型
专用挂具分为两种情况:一种是为大批量零件生产设计制作的专用挂具;另一种则是依据零件的复杂几何形状和特殊工艺要求而设计的专用挂具。
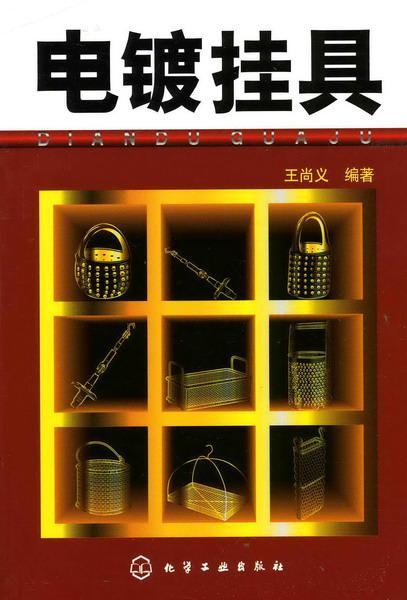
《电镀挂具》 王尚义编著&
通用挂具
通用挂具适用于多种零件和工艺。通用电镀挂具的形式和结构,应根据镀件的几何形状、镀层的技术要求、工艺方法和设备的大小来决定。例如,片状镀件在上下道工序之间会随镀液的阻力而漂落,在选用挂具时要将镀件夹紧或用铜丝扎紧。若镀件较重而有孔时,可选用钩状的挂具。使用要求如下:
(1)手工操作使用的挂具。装载重量一般为1~3kg。
(2)吊钩应有足够的导电面积,其型式应使导电良好。挂具吊钩应经常清洗。
(3)使用时,应注意轻装轻放,尽量不要损坏绝缘层。否则会造成挂具与工件抢电,致使工件出现局部镀不上或粗糙等现象,影响镀层质量。
(4)挂具使用后,要清洗干净,集中妥善存放备用。
(5)使用一段时间后的挂具,要及时处理,退除挂具上的镀层,以保证导电良好。挂具绝缘层出现裂纹,要及时修复或重新绝缘处理。
专用挂具
(1)双极性法镀内孔夹具。
(2)镀铬夹具。镀铬溶液氧化能力较强,挂具材料应稳定,可用钛或紫铜作挂具。夹具导电部分应有足够的横截面积,不发热。夹具结构以焊接形式连接,导电铜钩应弯成直角形。夹具与零件应尽量采用螺纹接触。内孔镀铬夹具阴阳极必须隔电。利用绝缘块(硬塑料板或有机玻璃)代替保护阴极。夹具的非工作面应进行绝缘,减少电流的消耗。零件装挂的位置,气体排除应最容易。挂具在保证适用的前提下,应尽量轻便、简单、通用、装卸方便。
小零件电镀用挂具
小零件可采用滚镀的方法进行电镀。若无滚镀条件,可用挂篮作为电镀工具。挂篮的骨架为黄铜或铁丝、底部和周围都采用金属丝网,网孔的大小以零件不从孔中漏出为标准,孔稍大一些有利于获得厚度均匀的镀层。为了改善镀层质量,提高沉积速度,可用钻孔的塑料板代替周围的金属网。
化学处理用挂具
钢铁零件磷化、氧化时,可以用挂具,也可以在挂篮里进行,一般零件尽量采用挂篮。在有起重设备的条件下,挂篮可大些。挂具全部用钢铁材料制作。不用铜或黄铜,以保证膜层质量,因为在这些溶液中会使铜溶解而沾污溶液,影响膜层质量。挂具的形式除了没有导电性能要求外,其它都和电镀相同。
酸洗所用的挂具和挂篮很容易损坏,应选择耐腐蚀性能好的材料或直接选用塑料制品。其形状与小零件电镀相同。
钢铁件的氧化不需通电,通常使用挂篮,只要求挂具有较高机械强度,耐蚀性较好,装卸工件简便即可。对于较精密工件或有外螺纹的工件,为防止相互碰撞,以采用挂具为宜。
铝和铝合金的挂具
铝件阳极氧化时,应采用铝和铝合金的挂具。挂具应具有弹性以将零件夹紧,防止由于接触松动处,形成不导电的氧化膜,而影响阳极氧化继续进行。
结构
挂具的结构一般都比较简单,由吊钩、提杆、主杆、支杆和挂钩五个部分组成。
吊钩
是挂具与极棒的连接结构,电镀时由它传递电流到挂具和零件上,因此,必须采用导电性能好的材料制作。吊钩和极棒应保持较大的接触面和良好和接触状态,以保证电流顺利通过。其截面积相当于挂具主杆材料相同的截面积。吊钩要承受挂具和镀件的全部质量,故要求有足够的机械强度。吊钩与主杆通常用相同的材料制作,两者可做成一体,也可分开制作,把它与极棒用钎焊或其它方法和挂具连接在一起。用钢或铝合金等制作的挂具,吊钩一般使用铜、黄铜,连接方式可用铆接和焊接。其尺寸,应根据阴极棒的直径来设计,使挂具在悬挂和取下时操作方便。提杆
位于主杆的上部并和主杆垂直,用焊接的方法与主杆相连。当挂具悬挂于镀槽时,提杆的位置应高出液面80 mm左右。操作时用提杆提取挂具。应具有足够的机械强度,截面积一般和支杆相同或稍大一些。主杆支撑整个挂具和所挂零件的重量,并通过主杆传递电流到各支杆和零件上。主杆的材料一般选用φ(6~8)mm的黄铜棒。支杆通常用焊接的方法固定在主杆上,工作时承受悬挂零件的重量,支杆的材料一般用φ(4~6)mm的黄铜棒。挂钩
一般都焊接在支杆上,有时也焊接在主杆上,用来悬挂或夹紧零件。其材料一般为钢丝、磷青铜丝。挂钩在挂具上的分布密度要适当。应使挂具上的零件绝大部分表面或重要表面能够朝向阳极,并避免压叠现象。一般中小型镀件之间间隔(15~30)mm,杯状镀件的间隔一般为直径的1.5倍。根据挂钩与镀件连接方式的不同,挂钩分悬挂式和夹紧式两种形式。
(1)悬挂式挂钩。镀件与挂钩一般采用自由悬挂法。即将挂钩挂在零件的孔内或适当的位置,零件挂上后既能活动又不致脱落,抖动挂具时还能转换其接触点。这种挂钩装卸方便,镀件上挂具印迹不明显。电镀中电流密度较小时,一般采用自由悬挂法。
(2)夹紧式挂钩。镀件与挂钩的连接靠弹性接触。一般在光亮电镀、镀铬等场合或采用较大电流密度时使用。它是利用挂钩的弹性夹住零件的某一部位,依靠接触压力使其导电良好。弹性的强弱由挂钩所用材质、线径、线长、板宽、板厚决定。
无论用哪种方式悬挂零件,都应保证零件在电镀时产生的气体顺利排出,以免产生的气体积聚某一部位形成“气袋”而影响镀层质量。比如有盲孔和凹形的零件悬挂时其口部应稍向上倾斜,塑料件要采用多个触点与挂钩接触。总之,挂钩的形式和悬挂的方式随零件的形状和电镀工艺条件来决。
外形尺寸
挂具的外形尺寸要根据零件和设备的大小来决定。合理的考虑挂具的外形尺寸,就能充分利用设备的有效容积,从而提高生产效率及保证电镀质量。
横截面积
若挂具截面积过小,则需要很长的时间才能使镀层厚度达到要求。若截面积过大,则会造成材料的浪费,所以挂具截面积的计算要合理。
挂具横截面积越大,允许电流密度值越小;横截面积越小,允许电流密度值越大。浸在溶液中时允许的电流密度值比不浸在溶液中时大。扁平排形挂具散热状况好,可以适当增大允许电流密度值。表面经过绝缘处理后的挂具,允许电流密度值比裸露时小。
材料选择
挂具应选择有足够的机械强度、电导性能良好、不易腐蚀的材料。常用的有钢、不锈钢、铜、钛、黄铜、磷青铜等。一般通过钢质挂具上的电流密度不宜超过1A/mm2;通过黄铜挂具上的电流密度不宜超过2~2.5A/mm2;通过紫铜挂具上的电流密度不宜超过3 A/mm2;通过铝及铝合金上的电流密度约为1.6 A/mm2。
绝缘处理
电镀挂具的绝缘处理,是指除了需要和零件接触有导电要求的部位外,其它部位都用非金属材料包扎或涂覆,使其成为非导体。这样可使电镀过程的电流集中在零件上,加快沉积速度,同时节约了金属材料和电能消耗。在挂具退镀和酸洗时,还可减少挂具的腐蚀,延长挂具使用寿命。
对于绝缘处理所用的材料,要求具有化学稳定性、耐热性、耐水性、绝缘性、机械强度和结合力、结合力强,机械强度较高、涂层可去除。
绝缘前应进行预处理,即去除挂具上的毛刺、焊垢,将其凹凸处整平。在支杆、挂钩等处施加压应力,延长挂具寿命。
包扎法
一般采用宽度为10~20mm、厚度为0.3~1mm的聚氯乙烯塑料膜带,在挂具需要绝缘的部位自下而上的进行包扎。包扎时将绝缘带拉紧并缓慢的转动挂具,缠扎第二层时压住第一层的接缝,最后用金属丝扎紧。在挂钩上也可用尺寸合适的聚氯乙烯塑料管套上,只留出需要和零件接触的部位。
用聚氯乙烯薄膜包扎的绝缘方法,在电镀生产中采用较普遍,但由于包扎过程中,塑料薄膜和挂具之间总有一些间隙,加上塑料容易热胀冷缩,溶液容易残留在里面,而使工序间溶液相互污染,故在使用上受到一定的限制。
浸涂法
挂具在浸漆前先进行除油、浸蚀和干燥处理,然后浸渍或在其表面涂刷一层防蚀绝缘漆。待漆膜完全干燥后,再将挂钩上需要和零件接触的部位用小刀刮去漆膜。常用的绝缘材料有过氯乙烯、聚氯乙烯、聚苯乙烯、聚乙烯防腐清漆、耐酸硝基漆和氯丁胶等。
过氯乙烯防腐清漆法:清除其表面的油污和氧化物,以提高漆层和挂具的结合力。再将清洁和干燥的挂具浸入过氯乙烯防腐清漆(G52-2)中,使挂具需要绝缘的部位附着一层清漆,然后放在空气中干燥10~20min,当第一层漆膜干燥后,再重复进行浸渍,涂覆的次数与电镀工艺有关,一般重复5~10次即可。当漆膜完全干燥后,将挂钩上需要和零件接触的部位用刀具除去漆层。这种绝缘处理的方法比较简单,过氯乙烯防腐清漆化学稳定性较好,能耐酸、碱,但它的耐热性能还不够理想,一般只适用于80℃以下的情况。
聚苯乙烯性能及使用温度条件与过氯乙烯相近,只是耐碱差,且结合力不够理想。
聚氯乙烯涂层耐酸、耐碱、耐热、耐磨性能均良好,适于温度较高或易受碰撞的场合。
氯丁胶具有聚氯乙烯涂层耐酸、耐碱、耐高温的所有优点,且不脱落,结合力强。涂后自然干燥,也可加温干燥。
沸腾硫化法
将挂具除油、除锈刷洗干净,加温到250℃左右,立即放入专用硫化桶中,利用挂具本身的余热,使塑料粉粘附并随之塑化在挂具上,形成一层均匀的薄膜。然后取出放在水中冷却(避免塑料长时期受热而老化)。若一次硫化后塑料薄膜厚度不够,可将挂具放回烘箱内,在加温到250℃后,重新进行硫化处理。若硫化后挂具余热不能使粘附的塑料塑化,可以在烘箱中保留片刻,再取出冷却。挂具需要导电的部位可用刀具轻轻刮去。为使塑料涂覆均匀,挂具应尽量减少棱角、焊渣及复杂的弯曲变形。由于塑化时温度很高,挂具需采用铜焊。
若要得到不同颜色的绝缘层,可在聚乙烯塑料粉中加入0.5 %的酞蓝、铬黄、铁红等颜料,来代替炭黑。沸腾硫化的工作条件是:加温至250~300℃;塑化温度 220~225℃;塑化时间8 min;也可用其它市售绝缘材料。
作用和要求
挂具在电镀生产中主要起导电、支撑和固定零件的作用,挂具和电极相连接,使电流较均匀地传递到零件上进行电镀。在某些情况下,由于溶液性能限制镀层的均匀分布,还可依靠挂具来弥补。
电镀挂具应具有足够的机械强度和良好的导电性能;并要求重量轻、面积小、坚固耐用、装卸零件方便、装载量适当等。
设计与制作
随着空军新装备的跨越式发展和电镀新材料、新工艺的应用,在航空维修工程中对零件进行电镀时,合理地设计与制作挂具,对于保证镀件质量,提高维修速度,降低劳动强度,减少污染物的带出和排放,提高军事效益和环境效益都有重要意义。
1.按照零件电镀的特点设计和制作挂具
(1)由于新装备零部件的电镀质量要求高,因此,电镀挂具的设计与制作也要有所提高才能跟上新装备发展的要求。
(2)除了按通用工艺规程进行电镀外,还要进行飞机战伤的应急抢修电镀,这就需要设计制作和储存必要的挂具,以备战时进行野战抢修电镀。
(3)航空维修中的电镀件,除部分通用和常用的成批件、新制批量件,可在自动线和滚镀机上完成外,还有相当一部分需要挂镀完成 比如某架飞机、某个部件维修时,需要电镀的零件只有几件、几十件,遇到这种情况,使用挂镀就可完成。因此,在挂具的设计制作时要充分考虑其批量和数量睛况,同时还要考虑挂具的通用性和专用性。
2.设计制作时应注意的问题
(1)挂具材料的选择
应按照零件形状、太小、基体材料、镀种及镀层要求进行设计、选择制造挂具的金属材料和非金属材料。不论采用什么材料、方法,都要使包扎和涂刷层表面均匀光滑,达到既要绝缘性能良好,又要让挂具出槽时槽液快速滴落回收。
(2)挂具材料应有足够的强度和导电截面
设计制作挂具时,应根据挂具所挂零件,首先计算出受镀件(包括阴极保护)的总面积和所需最大电流,然后根据最大电流密度的上限确定挂具的主杆及支杆的电流量,并选择材料的种类、粗细、厚薄等。对于多工序流水线使用的挂具,应按照流水线工序中的最大电流密度来计算。
有些挂具还要考虑有足够的强度和重量,保证零件在阴极移动和空气搅拌过程中接触良好,不该晃动的不能晃动,需要晃动的则要晃动灵活。
(3)挂具与零件要有良好的接触
挂具的设计如果不完美,装挂后与零件接触不良就会产生接触电阻,影响电流的传导作用,轻则导致触点周围没有镀层、镀层结合力不良、镀层厚度不均匀等质量问题,重则发生电烧伤零件,造成零件报废。
(4)使用方便,装挂布置要合理
挂具设计制作时要考虑使用方便。自动线上的挂具体积可适当大些,但要注意操作者装卸方便。
手工操作的要考虑体积、重量的大小等因素,以利于操作者在零件装夹、拆卸、上槽、下槽、提运时使用方便。