分类
钼钨合金含钼和钨两种元素的合金,它包括以钼为基的钼钨合金和以钨为基的钨钼合金系列。该种合金能以任何比例形成,在所有温度下均为完全固溶体合金。
铌钨合金以铌为基加入一定量的钨和其他元素而形成的铌合金。钨和铌形成无限固溶体。钨是铌的有效强化元素,但随着钨添加量的增加,合金的塑性一脆性转变温度将上升,晶粒也显著长大。因此,要得到高强度的铌钨合金,须适当地控制钨的添加量,同时还须适量加入细化晶粒、降低塑性一脆性转变温度的元素如锆和铪等。1961年,美国研制成功用于航天飞机蒙皮的Nb-10W-2.5Zr合金,以后又发展成为Nb-10W-1Zr-0.1C合金。70年代初,中国也研制成功NbWl0Zr2.5和NbWl0Zr1C0.1合金。
硬质合金硬质合金是最常见、最主要的一种钨的合金形式,有别于前面几款钨合金的是它是钨和碳、钴,因而它也常被称为钨钴合金。目前,工业领域应用最广泛的刀具基本都是硬质合金刀具,所以硬质合金这种钨合金也被称为是“工业牙齿”。
发展历史
1907年,一种低镍含量的钨合金问世,它是通过机械加工方法制备的,但是严重的脆性妨碍了它的应用。直到1909年,美国通用电器公司的库利奇(w.D.Coolidge)通过粉末冶金法制得 钨坯条,再利用机械加工生产出在室温下具有延性的钨丝,从而奠定了钨丝加工业的基础,也奠定了粉末冶金的基础。
然而这种“延性”钨合金在灯泡点燃后表现出明显的脆性。1913年,平奇(Pintsch)发明了钍钨丝(ThO2的 含量为1%~2%),从而使白炽灯丝的脆性大大降低。起初,灯丝的下垂(见钨丝的抗下垂性能)并不是一个问题,因为此时的灯丝是直丝,但1913年以后,兰米尔(Langmuir)将直丝改为螺旋丝,这样,当灯泡使用时,高的工作温度和自重的作用使灯丝下垂,因而纯钨和钍钨都难以满足使用要求。
为了解决钨丝下垂和寿命短等问题,1917年,柏斯(A.Pacz)发明了高温下“不变形”的钨合金。起初,他在制备纯钨时采用耐火坩埚焙烧WO3,无意中发现用这种WO3还原所得钨粉制成的
钨丝
螺旋,经再结晶后异常神秘地不再下垂。随后,经过218次反复实验验证,他终于发现在钨酸(WO3·H2O)中添加钾和钠的硅酸盐,经过还原、压制、烧结、加工等制得的钨丝,再结晶后形成相当粗的晶粒结构,既不软又抗下垂,这是最早的不下垂钨丝。柏斯的发现奠定了不下垂钨丝的生产基础,直到现在美国仍称不下垂钨丝为“218钨丝”,以纪念柏斯的这项重大发现。掺杂
钨合金的生产工序冗长,包括钨冶炼、粉末冶金制坯和塑性加工几个主要阶段。掺杂
钨合金的生产通常选用 仲钨酸铵(APT)
为原料。从钨精矿制取仲钨酸铵除了传 统的经典工艺外,20世纪50年代国际上开展了萃取法和离子交换法的研究,中国在70年代也采用了这些工艺,从而简化了工艺流程,提高了钨的回收率。20世纪60年代以来,许多国家都相继采用蓝色氧化钨掺杂工艺代替三氧化钨掺杂,从而提高了掺杂效果。钨粉的酸洗是20世纪60年代开始应用于生产的,其主要目的在于洗去钨粉中多余的掺杂剂、超细粉和部分有害杂质,从而改善加工性能,提高钨丝的高温性能。从20世纪60年代开始,孔型轧制法不断得到应用。孔型轧制是使坯料在一对旋转着的轧辊的孔 型中通过,在轧辊压力的作用下使断面减缩和长度延伸。虽然只有少部分 钨矿最终被做成灯钨丝和类似的产品,钨在科学上和技术上所承担的最重要的意义就是其研究成果向实际应用的转换。所获得的知识在粉末冶金新的领域,尤其是在硬质合金的制造上具有不可估量的价值。
用途
灯丝业钨最早用于制作白炽灯丝。1909年美国库利吉(W.D.Coolidge)采用钨粉压制、重熔、旋锻、拉丝工艺制成钨丝,从此钨丝生产得到迅速发展。1913年兰米尔(I.Langmuir)和罗杰斯 (W.Rogers)发现钨钍丝(又称钍钨丝)发射电子性能优于纯钨丝后,开始使用钨钍丝,至今仍然广泛使用。1922年研制出具有优良的抗下垂性能的钨丝(称为掺杂钨丝或不下垂钨丝),这是钨丝研究中的重大进展。不下垂钨丝是广泛使用的优异灯丝和阴极材料。50~60年代,对钨基合金进行了广泛的探索研究,希望发展能在1930~2760℃工作的钨合金,以供制作航天工业使用的耐高温部件。其中以钨铼系合金的研究较多。对钨的熔炼和加工成形技术也开展了研究,采用自耗电弧和电子束熔炼获得钨锭,并经挤压和塑性加工制成某些制品;但熔炼铸锭的晶粒粗大,塑性差,加工困难,成材率低,因而熔炼-塑性加工工艺未能成为主要生产手段。除化学气相沉积(CVD法)和等离子喷涂能生产极少的产品外,粉末冶金仍是制造钨制品的主要手段。
板材业中国在20世纪50年代已能生产钨丝材。60年代对钨的熔炼、粉末冶金和加工工艺开展了研究,现已能生产板材、片材、箔材、棒材、管材、丝材和其他异型件。
高温材料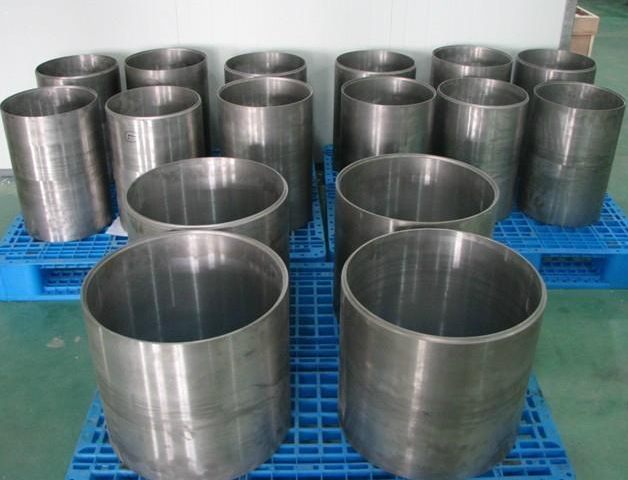
钨合金
钨材使用温度高,单纯采用固溶强化方法对提高钨的高温强度效果不大。但在固溶强化的基础上再进行弥散(或沉淀)强化,可大大提高高温强度,以ThO2和沉淀的HfC弥散质点的强化效果最好。在 1900℃左右W-Hf-C系和W-ThO2系合金都有着高的高温强度和蠕变强度。在再结晶温度以下使用的钨合金,采取温加工硬化的方法,使其产生应变强化,是有效的强化途径。如细钨丝具有很高的抗拉强度,总加工变形率为99.999%、直径为0.015毫米的细钨丝,室温下抗拉强度可达438公斤力/毫米在难熔金属中,钨和钨合金的塑性-脆性转变温度最高。烧结和熔炼的多晶钨材的塑性-脆性转变温度约在150~450℃之间,造成加工和使用中的困难,而单晶钨则低于室温。钨材中的间隙杂质、微观结构和合金元素,以及塑性加工和表面状态,对钨材塑性-脆性转变温度都有很大影响。除铼可明显地降低钨材的塑性-脆性转变温度外,其他合金元素对降低塑性-脆性转变温度都收效甚微(见金属的强化)。
钨的抗氧化性能差,氧化特点与钼类似,在1000℃以上便发生三氧化钨挥发,产生“灾害性”氧化。因此钨材高温使用时必须在真空或惰性气氛保护下,若在高温氧化气氛下使用,必须加防护涂层。
军事武器业随着科学发展进步,钨合金材料,成为当今制作军事产品的原料:如子弹、装甲和炮弹、弹片头、手榴弹,猎枪、子弹弹头、防弹车,装甲坦克,军航、火炮部件,枪支等。而钨合金造成的穿甲弹更是可以击穿大倾角的装甲和复合装甲,是主要的反坦克武器。
加工
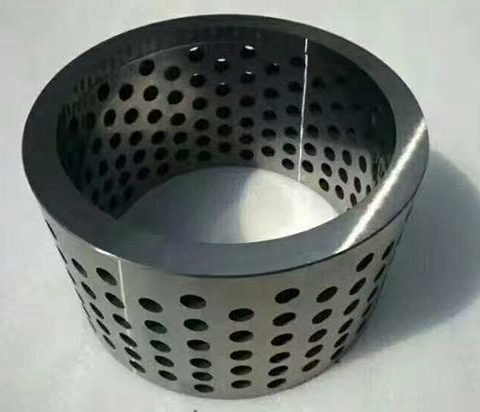
钨合金
钨的熔点高、硬而脆,加工困难,但只要有合理的工艺,钨可经粉末冶金制坯、挤压、锻造、轧制、旋压和拉拔等加工成材。随着钨的塑性加工程度的提高,其组织、抗拉强度和塑性-脆性转变温度大为改善坯料准备合格的坯料是钨材生产的关键之一,制好坯料首先要选用合格的钨粉末。粉末的特征(平均粒径、粒度分布、化学成分)、混料、成形和烧结工艺对坯料的成分、密度和微观结构有直接影响,并强烈地影响着产品加工和使用性能。
不下垂钨丝中添加的硅、铝、钾元素是在三氧化钨或“蓝钨”(为多种低价氧化钨的混合物)中以氧化物形式添加的,混合料常用含氢氟酸的溶液进行洗涤,以去除粉中杂质。生产丝和小片材的坯料多在压力机上成形,也可采用等静压制成形。
粉坯尺寸一般为12×12×400毫米,也有采用较大尺寸的圆棒、方棒或矩形棒。粉坯首先在氢气气氛中经 1200℃、1小时预烧使之具有一定强度和导电性后,再进行通电自阻烧结。
通电自阻烧结俗称“垂熔”,是钨加工中发展起来的方法。原理是将电流直接通过烧结坯,由于坯料本身的电阻而产生焦耳热,利用这种热使坯料烧结,烧结电流通常为熔断电流的90%。所得坯料为自阻烧结条(又称垂熔条)。可加工成丝材的垂熔条一般标准是控制断面晶粒数为每平方毫米约10000~20000个,密度为17.8~18.6克/厘米3。对于管材、片材或其他大规格产品, 常采用等静压制(压力在2500公斤力/毫米2以上)成形,在2300~2700℃的高温下于真空或氢气保护中烧结。
旋锻旋锻是生产钨丝坯料和细棒的常用塑性加工方法,不同尺寸的棒材于氢气气氛中加热到1400~1600℃,在不同型号的旋锻机上进行旋锻。开始道次变形量不宜过大,随后可适当增加变形量。旋锻变形过程中工件和模具间用石墨润滑。加工后的钨棒密度可达18.8~19.2克/厘米3。由于方坯锻成圆坯,各部位变形不同,使组织不均匀,此时应进行再结晶退火。旋锻棒材的最终直径为3毫米左右。
拉丝拉丝坯料可用旋锻法生产,也可用轧制法生产;轧制法生产的坯料道次变形量大,组织较均匀,有利于以后的加工。钨丝坯料拉制钨丝是用“温拉丝”方法。首先在链式拉伸机上拉至直径1.3毫米,而后分别经粗拉、中拉和细拉使直径达到 0.2、0.06和小于0.06毫米。随着直径减小,应使加热温度下降、拉丝速度提高。道次变形量一般在10~20%之间。
拉丝采用煤气-空气混合加热,温度为900~400℃。拉粗丝采用硬质合金模,拉细丝则采用金刚石模。模子材质、孔型、研磨技术对丝材质量有很大的影响,石墨润滑剂的质量、粒度、配比、涂敷方法同样影响丝材质量。
丝材直径的不均匀性是使用时断丝的最主要原因之一,有0.2~0.4微米的偏差就会使真空管中钨丝的寿命大大降低。细丝材的直径可以用重量法或真空标准电流法进行测定。在拉丝过程中,随着直径减小,变形抗力增大(如直径0.1~0.3毫米钨丝的断裂强度可高达350公斤力/毫米2),其塑性也相应降低。为了改善再加工性能,一般需要进行消除应力中间退火。此外,可采用电解腐蚀法将丝材加工成直径小于0.01毫米的细丝。
牌号标准
钨合金牌号标准:
AMS-T-21014
AMS-T-21014 | Class 1 | Class 1 | Class 2 | Class 2 |
配比 | 90W7Ni3Fe | 91W6Ni3Fe | 92W5Ni3Fe | 93W4Ni3Fe |
密度(g/cm3) | 17.1±0.15 | 17.25±0.15 | 17.50±0.15 | 17.60±0.15 |
热处理 | 烧结 | 烧结 | 烧结 | 烧结 |
抗拉强度(MPa) | 900-1000 | 900-1000 | 900-1100 | 900-1100 |
延伸率 (%) | 18-29 | 17-27 | 16-26 | 16-24 |
展开表格AMS-T-21014 | Class 3 | Class 3 | Class 4 |
配比 | 95W3Ni2Fe | 96W3Ni1Fe | 97W2Ni1Fe |
密度 (g/cm3) | 18.10±0.15 | 18.30±0.15 | 18.50±0.15 |
热处理 | 烧结 | 烧结 | 烧结 |
抗拉强度 (MPa) | 920-1100 | 920-1100 | 920-1100 |
延伸率(%) | 10-22 | 8-20 | 6-13 |
展开表格Anviloy
产品 | 正常配比 | 密度 (g/cm3) | 极限抗拉强度 (N/mm2) | 硬度 (HRC) | 应用 |
Anviloy 1150 | 90%W4Mo4Ni2Fe | 17.25 | 965 | 34 | |
Anviloy 4200 | 93%WNiFeMo | 17.8 | 885 | 30 | 压铸件 |
Anviloy 4000 | 90%WNiFeMo | 17.3 | 960 | 32 | 压铸工具 |
Anviloy 4100 | 86%WNiFeMo | 16.7 | 1075 | 36 | 压铸工具 |
Mil-T-21014
等级 | Mil-T-21014 |
Class1 | Class 1 | Class 2 | Class 3 | Class 3 | Class 4 |
配比 | 90%W,6%Ni4%Cu | 90%W,7%Ni3%Fe | 92.5%W,5.25%Ni2.25%Fe | 95%W,3.5%Ni1.5% Cu | 95%W,3.5%Ni1.5%Fe | 97%W,2.1%Ni0.9%Fe |
密度 (gm/cc;lbs/in3) | 17;0.614 | 17;0.614 | 17.5;0.632 | 18;0.65 | 18;0.65 | 18.5;0.668 |
硬度 (RC) | 24 | 25 | 26 | 27 | 27 | 28 |
极限抗拉强度 (PSI) | 110,000 | 120,000 | 114,000 | 110,000 | 120,000 | 123,000 |
展开表格NAVY MIL-T-21014:钨基零件, 高比重金属 (烧结或热压), 镀层, 电镀铬。
ASTM B 777-99
Class | 1 | 2 | 3 | 4 |
钨比例 % | 90 | 92.5 | 95 | 97 |
密度(g/cc) | 16.85-17.25 | 17.15-17.85 | 17.75-18.35 | 18.25-18.85 |
硬度 (HRC) Max | 32 | 33 | 34 | 35 |
极限抗拉强度 | ksi | 110 | 110 | 105 | 100 |
Mpa | 758 | 758 | 724 | 689 |
展开表格其他加工
钨的管材可采用烧结坯料直接挤压,挤压管坯或粉浆挤压烧结管坯还经旋压加工。旋压还可生产钨的异型制品。大直径的棒材多采用挤压或轧制工艺生产。
切削加工钨质硬且对缺口敏感,切削加工困难,要求使用硬质合金刀具。为防止产生切削裂纹,常把工件加热到塑性-脆性转变温度以上进行切削,并要严格控制切削操作程序。钨的研磨需要用特定型号的砂轮轻磨,且需要冷却,否则会产生龟裂。厚度在 0.2毫米以上的钨片材进行冲压和剪切前要预先加热,超过一定厚度的板材,不能剪切,往往需要用砂轮切割。
板材轧制钨板轧制可分热轧、温轧和冷轧。由于钨的变形抗力大,普通的轧辊不能完全满足钨板材轧制的要求,应使用特种材质的轧辊。轧制时,轧辊要预热,根据不同的轧制条件,预热温度为100~350℃。坯料的相对密度(实际密度与理论密度之比)大于90%时才可加工,坯料密度在92~94%时加工性能良好。热轧的开坯温度在1350~1500℃之间,开坯的变形工艺参数选择不当,坯料会产生分层。温轧的开始温度为1200℃,厚度为8毫米的热轧板,经温轧可达到0.5毫米。由于钨板变形抗力大,轧制时轧辊辊身弯曲变形,使板材沿宽度方向上厚度不均,换辊或换轧机时,板材可能因各部位变形不均匀而开裂。0.5毫米厚度板材的塑性-脆性转变温度还在室温或室温以上,片材呈脆性,应在200~500℃将片材轧制成0.2毫米。轧制后期,钨片薄而长,为保证板材加热均匀,常涂石墨或二硫化钼,不仅有利于板材的加热,而且加工时还有润滑作用。
设计
设计钨合金时,(1)为提高钨合金的塑性,必需降低其中氧和碳元素的含量;(2)细化晶粒和热加工也是降低钨合金%BTT的有效方法:(3)考虑到钨合金的综合性能,Re和Mo是最有效的固溶强化元素,但在核辐射环境中应用时,Re元素除外;(4)难熔金属碳化物是最有效的第二相强化颗粒。(5)为实现钨基复合材料的工业化生产,必需降低其制备和加工成本,则原位反应和反应浸渗法是制备钨基复合材料的理想方法。
钨合金电镀
油田设备的“腐蚀”与“磨损”被称为两大世界级难题,全国约2.92万口油井都存在不同程度的腐蚀与磨损,随着我国油气田开发年限和设备使用年限的增长更是每况愈下。另外,高含硫原油进口量大幅增加,炼制设备的腐蚀问题同样日益突出。更加可怕的是,因腐蚀和磨损对设备安全稳定运行带来的不利影响会越来越突出。
在几种主要电镀工艺中,电镀铬工艺耐磨,成本低,但环境污染严重,且不耐氯离子腐蚀;化学镀镍磷工艺耐腐蚀却不耐磨,成本也高;热喷涂工艺各项技术指标均不错,可是生产成本高,很难大范围推广。
据我国知名青年化工专家,美国加州大学博士后,湖南大学博导何凤姣教授指出:“对磨损、腐蚀造成零件失效的研究表明,这些失效大都发生在材料表面。利用表面工程的技术手段对材料表面进行处理,改善材料的表面性能,会有效地延长零件使用寿命,因此,表面工程在石油石化工业中具有重要地位。”
“从目前来看,只有钨合金电镀技术性能大幅提高,其硬度与耐磨性和电镀铬相当,但是耐酸耐碱,生产成本低廉,而且可以根据石油井下的具体作业情况配置电镀液,实施相应的电镀工艺,满足其作业要求。现在,同样的环境下,采用钨合金电镀的设备使用寿命高出好几倍。”何凤姣教授解释说,“钨合金电镀之所以性能如此优越,是因为钨合金电镀后所得的镀层是新的合金材料,镀态为非晶结构,经不同的热处理工艺,可转变为非晶夹 杂纳米晶或纳米晶结构,经国家权威部门检测,该合金具有很好的耐磨性,很好的耐酸、耐碱、耐盐雾性能,以及优异的抗高温氧化性能,与基底材料有很好的结合力。”
钨合金电镀工艺一举解决腐蚀与磨损两大难题,据统计,我国每年油井管300多万吨,而高技术含量、高附加值的高端油井管,如抗H2S、Cl-防腐油管等几乎完全依靠进口,每年进口油管60万吨,价值300亿元以上。该成果已经取得8项专利许可,获得了国家机械工业科学技术奖一等奖,获得国家重点新产品证书。更让何教授高兴的是,国家环保总局将该技术列为国家重点环境保护实用技术(A类),列为国家鼓励发展的资源节约综合利用和环境保护技术。
钨合金电镀工艺在石油机械行业的应用,不但可以解决电镀铬带来的污染问题,更重要的是可以提高中国石油机械制造业各类关键性零部件产品的性能,给整个石 油机械制造业带来了变革,促进了产业链的整体升级,特别是防腐抗硫油井臂和抗硫钻杆可应用于H2S含量大于等于15万PPM,CL-含量达150克/L的 极端腐蚀环境,使我国在该产业上达到国际领先的水平,解决了我国高端钻采设备依赖国外进口设备的现状。
相关知识
按照用途不同,钨合金分为硬质合金、高比重合金、金属发汗材料、触头材料、电子和电光源材料。
掺杂钨丝是在钨粉中添加 1%左右的硅、铝和钾的氧化物,在垂熔(自阻烧结)过程中,添加剂氧化钾挥发,在材料内部形成气孔,气孔经加工后沿轴向拉长;退火后,拉长气孔形成弥散的平行于丝轴的气泡行,这种弥散的气泡俗称为钾泡。钾泡阻碍钨晶粒的横向长大,提高钨的高温抗下垂性能,还可改善再结晶后的室温塑性,有利于绕丝和运输贮存。中国掺杂钨丝依高温蠕变值有WAl1、WAl2、WAl3三种牌号。
在W-ThO2系合金中,由于添加适量的热稳定性好的弥散的ThO2质点,不仅可以降低电子逸出功,还可抑制钨晶粒长大,使材料具有很高的再结晶温度、优异的高温强度和抗蠕变性能。钨钍合金不仅是广泛使用的热电子发射材料,而且是优异的电极材料。
钨铼合金中,铼的添加,不仅能提高材料强度,提高合金的再结晶温度约200~400℃,使二次再结晶后塑性好、晶粒长大缓慢,而且可以显著降低塑性-脆性转变温度。添加的铼如超过30%,就会损害合金的加工性能。钨铼合金还具有较高的热电势,在2200℃下,其热电势与温度成直线关系。钨铼热电偶测量温度可高达3000℃,是优异的高温热电偶材料。
我国硬质合金产业存在的主要问题:
一是企业规模较小,产业集中度不高。
二是科技投入较少,缺乏高端技术人才,技术研发能力较弱。我国硬质合金工业在科技方面的投入不到销售收入的3%,科技研发水平不高,原创性核心技术成果较少。
三是产品质量水平较低,产品结构有待调整。我国硬质合金产量占世界总产量的40%以上,但硬质合金销售收入不足全球的20%,主要是由于高性能超细合金、高精度高性能研磨涂层刀片、超硬工具材料、复杂大异制品、精密硬质合金数控刀具等高附加值产品产量较少、深加工配套不足以及品种不全所致。