简介
通常把淬火裂纹按图分成宏观裂纹和微观裂纹两大类:
宏观裂纹由第一类内应力所引起,第一类内应力有四种分布形式,因此,由其引起的宏观裂纹也有四种类型,即:纵向淬火裂纹、横向淬火裂纹、网状淬火裂纹及径向淬火裂纹。
显微裂纹是由第二类内应力即微观应力所引起,一般多分布在片状马氏体中,此与片状马氏体点阵的正方畸变密切相关,它是马氏体片在交界处相互顶撞所产生的正应力超过垂直于轴的(001)立方面的断裂强度时而萌生的微观裂纹。
引起淬火裂纹的主要因素有:淬火加热方式和加热速度控制不当、加热不均匀、淬火温度过高、淬火时冷却方式不当、冷却速度过快、冷却不均匀;冷却介质选用不当;淬火前,工件未进行预备热处理或处理不当;回火不及时;材料缺陷或工件表面缺陷所引起的高应力集中等。
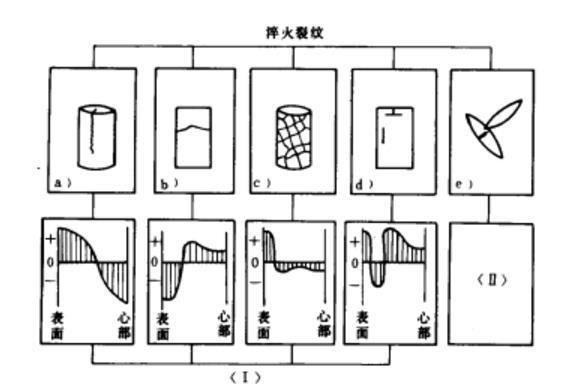
淬火裂纹类型与应力分布方式的关系
图中:I:第一类内应力;Ⅱ:第二类内应力a)纵裂;b)横裂;c)网状裂纹;d)径向裂纹;e)显微裂纹生成及类型
纵向裂纹
纵向裂纹又称轴向裂纹,它是由工件表面伸向心部的深度较大的裂纹,这种裂纹产生于轴件表面最大拉应力处。生产实践证明,在完全淬透的轴件上易于产生纵向裂纹,而且随着淬火温度的提高,形成这种裂纹的倾向也随之增大。图为载重车齿轮轴淬火时产生的纵向裂纹。这种裂纹的特征深而长,在零件上可分布一条或几条。
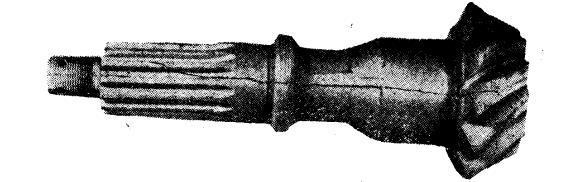
齿轮轴纵向淬火裂纹
横向裂纹与弧形裂纹横向裂纹的特征是裂纹的方向与轴件的轴向相垂直。从应力角度分析属于热应力所引起的裂纹。这类裂纹常常发生在淬火时未能淬透的大型轴件上。如轧辊等大型锻件。而且这些大锻件中常常存在汽泡、夹杂、发纹、白点等缺陷。在热处理应力作用下,这些缺陷将成为横向裂纹的裂纹源,随之逐渐扩展。
弧形裂纹的特点是裂纹主要产生于工件的内部,或在尖锐棱角及孔洞附近,即容易形成应力集中之处,并以弧带状分布。图为曲轴轴颈油孔附近产生的弧形裂纹。
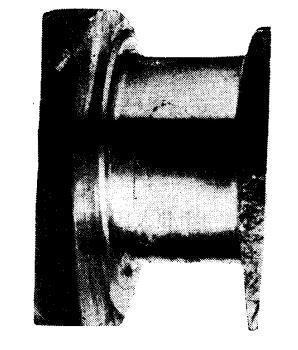
曲轴轴颈油孔附近的弧形裂纹
当轴类零件表面淬火时,在硬化层与未硬化层之间的过渡区存在着较大的残余拉应力,易于形成过渡区裂纹。这种裂纹将由过渡区向表面扩展,而在表面呈现弧状。不论是横向裂纹还是弧形裂纹,它们的应力分布特征是表面受压应力。距表面一定距离处应力发生突变,即压应力变为拉应力状态。弧状裂纹首先产生在拉应力最大的峰值区域内。
剥离裂纹
所谓剥离裂纹是指产生在工件表面层很薄的区域内,且平行于表面而分布的。轴件绎化学热处理后,沿扩散层出现的表面剥落。或表面淬火的轴件其硬化层的剥落均属于剥离裂纹。图为发动机曲轴表面淬火后产生的剥离裂纹。
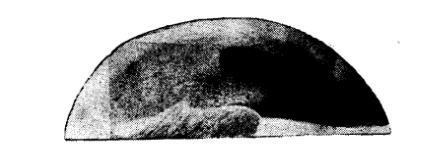
曲轴表面层的剥离裂纹
这类裂纹的产生是由于表面层淬成马氏体组织时体积膨胀受到过渡层和心部的牵制,使得马氏体层的轴向、切向均呈现出压应力,而在邻近的过渡层内呈现拉应力,就在从拉应力向压应力急剧过渡的极薄区域内产生剥离裂纹。一般情况下该裂纹隐藏在平行于表面的次层之中。严重时造成表面剥落。上述三种裂纹是轴类零件淬火时常见的开裂形式,有时个别者也会产生网状裂纹或显微裂纹。
特征
淬火裂纹的特征
在淬火过程中,当淬火产生的巨大应力大于材料本身的强度并超过塑性变形极限时,便会导致裂纹产生。淬火裂纹往往是在马氏体转变开始进行后不久产生的,裂纹的分布则没有一定的规律,但一般容易在工件的尖角、截面突变处形成。
在显微镜下观察到的淬火开裂,可能是沿晶开裂,也可能是穿晶开裂;有的呈放射状,也有的呈单独线条状或呈网状。因在马氏体转变区的冷却过快而引起的淬火裂纹,往往是穿晶分布,而且裂纹较直,周围没有分枝的小裂纹。因淬火加热温度过高而引起的淬火裂纹,都是沿晶分布,裂纹尾端尖细,并呈现过热特征:结构钢中可观察到粗针状马氏体;工具钢中可观察到共晶或角状碳化物。表面脱碳的高碳钢工件,淬火后容易形成网状裂纹。这是因为,表面脱碳层在淬火冷却时的体积胀比未脱碳的心部小,表面材料受心部膨胀的作用而被拉裂呈网状。
非淬火裂纹的特征
淬火后发生的裂纹,不一定都是淬火所造成的,可根据下面特征来区分:
淬火后发现的裂纹,如果裂纹两侧有氧化脱碳现象,则可以肯定裂纹在淬火之前就已经存在。淬火冷却过程中,只有当马氏体转变量达到一定数量时,裂纹才有可能形成。与此相对应的温度,大约在250℃以下。在这样的低温下,即使产生了裂纹,裂纹两侧也不会发生脱碳和出现明显氧化。所以,有氧化脱碳现象的裂纹是非淬火裂纹。
如果裂纹在淬火前已经存在,又不与表面相通,这样的内部裂纹虽不会产生氧化脱碳,但裂纹的线条显得柔软,尾端圆秃,也容易与淬火裂纹的线条刚健有力,尾端尖细的特征区别开来。
要点
淬火的目的是冷却奥氏体,不使其转变为珠光体和贝氏限,以获得马氏体组织。为此,必须如前面所提到那样以高与上临界冷却速度的冷却速度进行冷却。
另一方面为了减少淬火变形和防止淬火裂纹产生,各部分的冷却速度要尽可能均匀。总之,必须避免急冷。
如果这时候处理得好,就能够在获得马氏体的同时而小产生裂纹和弯曲。
1、即使快速冷却同样得到良好效果
形状简单的工件不易产生开裂和弯曲。零件设计避免锐角、断面突变和采取对称形状就能减轻裂纹,弯曲的发生。
2、要均匀冷却
因为棱角、薄壁等部分容易冷却应使之缓冷,反之凹部和厚壁部分则使之加速冷却。
此外,淬入到冷却剂中的方式和摆动方式,对获得均匀冷却具有重大的作用。
3、即使缓慢冷却同样得到良好效果
如果改变冷却剂,从水冷到油冷和从油冷到空冷,各部分的温差当然就小,裂纹和弯曲也将减少。这样,淬火,如果用上临界冷却速度小、淬透性好的钢进行淬火就能防止缺陷。
4、临界区域快冷、危险区域缓冷
淬火时,奥氏体→珠光体(贝氏体)的转变发生在550℃以上的冷却曲线与COT曲线鼻部接触的情况已经同时加以说明。所以在这个区域必须以高于临界速度的冷却速度进行冷却。
在这以后,如所了解那样,由于贝氏体的转变开始线的时间远在右侧,由此可以理解缓慢冷却是合适的。
因为造成裂纹弯曲等特殊问题的相变应力发生在Ms点以下构温度区现在这个区域内进行缓慢冷却使得各部分温度差小,就能抑制和降低相变应力的发生。
总之,如做到在临界区域快速冷却,危险区域缓慢冷却,就能够进行不发生裂纹,不发生弯曲而又充分硬化的理想的淬火。后面介绍的断续淬火即其方法之一。
其次,在保持一定温度的热浴中淬火的等温淬火是一种十分有效的方法。
实例探讨
1、轴,40Cr,经锻造、淬火后发现裂纹。裂纹两侧有氧化迹象,金相检验,裂纹两侧存在脱碳层,而且裂纹两侧的铁素体呈较大的柱状晶粒,其晶界与裂纹大致垂直。结论:裂纹是在锻造时形成的非淬火裂纹。
当工件在锻造过程中形成裂纹时,淬火加热即引起裂纹两侧氧化脱碳。随着脱碳过程的进行,裂纹两侧的碳含量降低,铁索体晶粒开始生核。当沿裂纹两侧生核的铁素体晶粒长大到彼此接触后,便向离裂纹两侧较远的基体方向生长。由于裂纹两侧在脱碳过程中碳浓度的下降,也是由裂纹的开口部位向内部发展,因而为铁素体晶粒的不断长大提供了条件,故最终长大为晶界与裂纹相垂直的柱状晶体。
2、半轴套座,40Cr,淬火后出现开裂。金相检验,裂纹两侧有全脱碳层,其中的铁素体呈粗大柱状晶粒,并与裂纹垂直。全脱碳层内侧的组织为板条马氏体加少量托氏体,这种组织是正常淬火组织。结论:在加工过程中未经锻造,因此属原材料带来的非淬火裂纹。
3、齿轮铣刀,高速钢,淬火后在内孔壁上出现裂纹。金相检验,发现裂纹附近的碳化物呈不均匀的带状分布。结论:这是由于组织不均匀所造成的淬火裂纹。
当钢的显微组织中存在碳化物聚集时,这些地方碳和合金元素的含量比较高,造成临界温度降低。因此,即使是在正常的温度下进行淬火加热,对于碳化物聚集处来讲,加热温度已显得过高了。其结果是这些地方出现过热组织,降低了钢的强度,淬火冷却时,在应力作用下产生开裂。
高速钢的碳化物不均匀性是这种钢的重要质量指标之一。为减少或预防这类缺陷发生,冶金厂和使用厂都在不断采取措施,如使用厂用改锻工艺来均匀组织。当碳化物不均匀性的改善程度受到限制时,可在保证硬度的前提下采用较低淬火加热温度来避免过热组织产生。
4、WCrV钢制模具,高温盐浴中加热后油冷,发现开裂。从裂纹特征上看是冷却过快所致。因工件截面较大,冷却时内外温差也大,当表面转变为马氏体时,内部仍处于奥氏体状态,以后的冷却过程中才逐步转变为马氏体,致使表层受内部体积胀大的作用承受很大的拉应力而开裂。因此,可以判断为淬火裂纹。