概述
机械部件应用减摩材料的目的,主要是要求尽可能低的摩擦系数,以降低摩擦损耗,提高传动效率。对于减摩材料除了其有低的摩擦系数外,还应具有:
1.较好的耐磨性、抗粘着性和磨合性;
2.良好的顺应性和嵌合性。
3.足够的强度。
4.导热性好、热膨胀系数小、抗腐蚀好,与油膜的吸附能力强。
顺应性是材料的表层对制造误差、受载变形和表面粗糙度的适应性能。嵌合性表示将外部杂质和硬颗粒嵌入摩擦表面而不外露以防擦伤对偶表面,影响性能。通常,硬度低、塑性好和弹性模量低的材料,其顺应性的嵌合性也较好。
减摩材料是一类古老而用途又十分广泛的、机械制造工业中不可缺少的工业用材。很早以前采用熔炼技术已可生产的锡基轴承合金(又称为锡基巴氏合金)便是一个典型代表,随后根据各种不同工况的要求,又开发出铝基、铜基等多个系列的减摩合金。由于采用熔炼技术生产减摩合金需用大量较贵重的有色金属如Sn、Cu、Sb等,而且由此加工成减摩零部件(如轴承、轴瓦)其合金的有效用量又很少,因此采用粉末冶金技术开发粉末冶金铁基、铜基减摩材料类型的零部件便有显著的优越性。为满足各种不同工况的要求,采用粉末冶金技术开发各种新型减摩材料便成为新型减摩材料研制的一个重要发展方向,从而导致一系列具有减摩性能的新型粉末冶金减摩材料的出现。
粉末冶金减摩材料是用来制造各种耐磨损的滑动轴承、轴瓦、活塞环、滑块、滑板及精密机床导轨等的材料,其中以滑动轴承用量最多。要求其具有低的摩擦系数、高的耐磨性能和足够的强度。粉末冶金减摩材料的摩擦系数很低,因材质不同而异,一般铁基减摩材料润滑时的摩擦系数为0.01~0.1,而铜基含油轴承在润滑的情况下对钢的摩擦系数可以小到0.004~0.008。这类材料是由具有一定强度的金属基体和起减摩作用的润滑剂所组成。基体通常为Fe、Cu、Al及其合金;减摩润滑剂有软金属铝、石墨和Fe、Mo、W、Zn的硫化物、硒化物以及氟塑料、玻璃等。由于采用粉末冶金技术可以在较大范围内调整基体和减摩剂的成分及含量,因而粉末冶金减摩材料的性能一般都优于熔炼合金的性能。
粉末冶金减摩材料可以分为多孔自润滑材料和致密减摩材料两大类。前者如各种含油轴,后者如粉末冶金铜铝轴瓦,若按基体材质分类,粉末冶金减摩材料可分为:铁-石墨材料、青铜-石墨材料、铝基减摩材料、金属-塑料、双金属铜铝轴瓦材料、减摩不锈钢、镍基和银基固体自润滑材料、金属-玻璃、难熔碳化物基减摩材料等等。
由于粉末冶金减摩材料是一种自润滑材料,具有很好的减摩性能,凶此广泛应用于农机、纺织机械、拖拉机、汽车、机床、运输机械、飞机、坦克、电机、食品工业设备、各种仪器仪表、电子计算机等领域。
我国一般粉末冶金减摩材料如铁基、铜基减摩材料在不少粉末冶金厂已成为主导产品,并已有几十年的生产历史,较好地满足了我国各行各业发展的部分需求。近20年来随着国民经济建设,特别是军事工业的发展,对减摩材料提出了一系列更高更新的要求,而且许多特殊性能只能采用粉末冶金技术才能研制出相应的高性能材料,我国在这方面取得了一系列可喜的重大进展。
对减摩材料的要求
摩擦(friction)、磨损(wear)与润滑(lubrication)统称摩擦学。据统计,大约有三分之一以上的世界能源消耗在摩擦上,大约有80%的破坏零件是由磨损造成的。摩擦学的应用范围特别广泛,一般机械里,如滑动轴承、滚动轴承、齿(蜗)轮传动、带传动、摩擦离合器和制动器、锻模及轧辊、切(磨)削工艺、弹性密封、机床导轨、轮胎在路面上滔车,车轮在铁轨上打滑等都存在摩擦学问题,甚至螺纹联接、铆接、轴毂联接里也发生微动磨损。机械设计中的摩擦问题大体分为减摩和摩阻两类,要求减摩的设计包括润滑设计和磨损设计,润滑设计有:运动副材料选配,润滑剂选择和结构合理性设计,磨损设计有:希望接触面磨损轻,磨损率低;要求摩阻的设计希望摩阻(摩擦)大,耐磨损,发热少和散热及时等。
对一切减摩材料的基本要求是:摩擦系数低;耐磨性高;有足够的韧性,没有脆性断裂的可能性;最佳的体积强度和表面强度,从而把表面层的高强度与摩擦偶件的易磨合性结合起来;有构成二次组织的能力,以提高摩擦表面的抗咬合性;材料中贮存固体或液体润滑剂等等。对减摩材料的要求由材料的工作条件所决定。对于具体用途的材料,还要求有特殊的性能。例如,化学、纺织、食品等工业部门需要在耐腐蚀介质条件下工作的减摩材料;火箭和低温技术需要在高真空以及接近绝对零度温度条件下工作的减摩材料;涡轮制造和连续铸钢设备则需要能在较高温度下工作的减摩材料等等。轴承用途所决定的工作参数,可以在很宽的范围内变化:滑动速度由几毫米/秒到100米/秒以上,载荷由0.1MPa到10~20MPa以上,温度从低温到1000℃以上。根据上述情况,不可能制造出一种能在各种不同用途的摩擦部件中都能使用的减摩材料。因此,必须研制出供规定条件下使用的各种不同的减摩材料。以往广泛采用的铸造方法制造的金属减摩材料,在许多情况下对于制造符合特殊工作条件要求的减摩材料是无能为力的。采用聚合物基材料,为较好地满足用最佳性能的材料装备摩擦部件的要求,增加了部分可能性。采用粉末冶金方法使问题得到了根本的解决。
从上述固体润滑的基本概念中已知,层状固体如石墨或二硫化钼等应用于滑动表面,摩擦和磨损会大大降低,石墨在干净表面滑动时,摩擦系数为0.1~0.2。但石墨用作固体润滑时主要困难之一是如何保持连续供应石墨,以便在两个滑动表面起固体润滑剂作用。起始的想法是将石墨混入滑动元件之一的基体中以提供两表面间的石墨,在最佳状况下,金属-石墨材料变成了自润滑剂。这就是粉末冶金方法解决问题的独到之处。其次,烧结减摩材料可以控制孔隙度,将油浸渍于孔隙可进行自润
常用金属减磨材料
巴氏舍金巴氏合金是最早应用于滑动轴承上的减摩材料(它是一种以锡或铅为基体的软合金),因最初由E.Babbitt(1839年)发明而称为巴氏合金,其成分含有82%~84%锡,5%~6%铜和11%~10%锑。后来将所有锡、铅基合金均称为巴氏合金。又因为它主要用于轴瓦,故又称为轴承合金。按组成的主要元素分,有锡基和铅基两类。
锡基合金的硬度较低(HB13~32),熔点也较低(240~320℃),当温度升高时,合金表面软化,起着润滑的作用,而且磨合容易。锡基轴承合金有良好的减摩性能,同时摩擦系数和膨胀系数小,塑性和导热好等优点,但疲劳强度低。疲劳强度的值与工作温度和合金层的厚度有关,降低温度和减小厚度都会提高疲劳强度,但厚度小于1mm时,由于浇铸时沿SnSb(锑化锡)晶界易出现裂纹,反而大大降低疲劳强度,故厚度不宜小于3mm。另外,合金中锑、铜含量不宜太多,否则在强度和耐磨性提高的同时,却使塑性和韧性恶化。
铅基合金以铅为主,含有适量的锑(10%~18%)和锡(0~20%)也是一种在软基体上分布着硬质点的轴承合金。该合金的成本低高温强度好,有自润滑性,但耐磨性、导热性以及钢背的附着能力不及锡基合金,可用于载荷不大和转速不高的场合。锡基和铅基巴氏合金的化学成分及性质见下表。
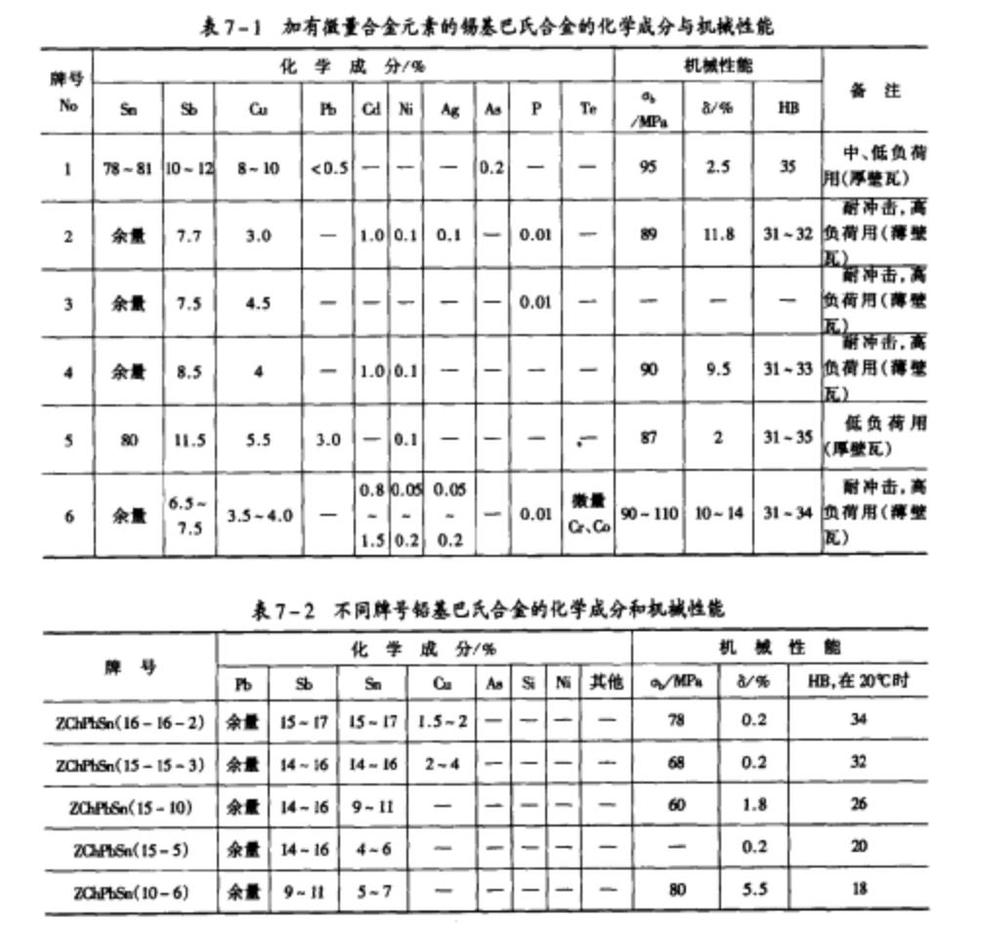
巴氏合金化学成分与性能
铜基轴承合金用作减摩材料的铜基合金主要有锡青铜和铅青铜。锡青铜是指含有5%~15%的锡以及少量锌、铅等元素的铜合金,加锌可使基体强度提高,加铅可增加合金的抗粘着性和顺应性,锡青铜的机械强度较高,减摩性和耐磨性也较好,适宜于制造重载轴承。
铅青铜是一种硬基体软质点型的轴承合金,其成分有30%左右的铅,其余由铜组成。铅青铜的承载能力和疲劳强度较高,能在250℃以下的温度正常工作,但顺应性和嵌合性较差,也不耐腐蚀。
铝基轴承合金铝基合金是最近几十年发展起来的一种新型减摩材料,其特点是比重小,导热性好,疲劳强度高和耐磨性好,且原料充足,价格低廉。但热膨胀系数大,抗胶合性、嵌合性与顺应性较差。得到应用的有铝锑镁轴承合金和高锡铝基轴承合金。前者的成分为3.5%~4.5%锑,0.3%~0.7%镁,其余为铝,铝为软基体,铝锑化合物(AISb)为一均匀分布的硬质点,加人镁能提高合金的屈服强度。铝锑镁轴承合金适用于载荷不超过20N/mm及滑动速度不大于10m/s的滑动轴承。
高锡铝基轴承合金的成分为20%的锡和1%的铜,其余为铝,该合金的显微组织以铝为硬基体,均匀分布着软的锡质点,添加的铜溶于铝中使基体强化。该材料适用于载荷达28N/mm,滑动速度在13m/s以下的滑动轴承。
多层合金减摩材料该材料为双金属、三金属等结构,各种金属的性能具有互补性,以满足机器高速、重载等工况下的使用要求。
粉末冶金减摩材料该材料是用金属粉末与具有减摩性能的非金属固体粉末,按一定比例,经混合后压制成型,再经烧结和整形得到的一种具有多孔性组织的材料。一般孔隙度在15%~20%范围。如用浸渍方法使孔隙中充满润滑油,便成为一种具有自润滑性能的减摩材料,含油轴承即为这种材料的一种制品。当轴颈转动时,由于轴颈在接触区有泵吸作用,迫使孔隙中的润滑油经毛细管作用被吸至轴承接触表面;同时由于摩擦热的作用,油的体积膨胀大于金属而被挤至摩擦表面,从而起着润滑作用。当停止转动后,温度下降,由于毛细管作用又将油吸回到孔隙中。因而这是一种具有自润滑、减摩及耐磨并有吸振作用的减摩材料。
常用的粉末冶金减摩材料有铜基和铁基两类。
铜基的主要成分为85%~89%铜、10%锡、0~3%铅和1%~5%石墨,该材料自润滑性能、减摩性能均较好,硬度低,易跑合。
铁基的主要成分为96%以上的铁粉,其余为石墨粉。其特点是承载能力高,价格低。
利用粉末冶金技术可以使制成的减摩材料具有各种特殊的功能,例如能在重载下工作的极高强度材料,可在高温下工作而具有高抗氧化性能的材料,以及在真空无润滑条件下具有良好抗擦伤能力和低摩擦系数的材料等。所以近年来粉末冶金减摩材料都是以较高的速度增长,而且适用的速度、载荷和温度范围也在扩大。除铜基和铁基外,在特殊的工作条件下还可用铅基、锌基、锡基、银基和镍基材料。所用的固体润滑剂除石墨外,还可添加硫、硫化物、钼、钒及其他金属硒化物、氟化物、卤化物等。为了提高耐磨性和强度,可添加锰、铬、镍和钼等合金元素,使材料获得可改善减摩性能的多相组织。
常用非金属减摩材料
砂无机和有机材料都具有减摩性能,可用于在干摩擦或边界摩擦条件下工作的摩擦元件,其中应用较多的是高分子聚合物和各种工程塑料。
聚酰胺通称为尼龙。它具有较高的机械强度和较好的耐磨性及自润滑性能,摩擦系数μ=0.25,易成型,价格低,耐磨蚀。可在无润滑条件下工作。然而尼龙热膨胀系数大,导热性差,有吸湿性。不宜在潮湿或温度变化较大的环境下工作,在有泥沙或尘土的环境中工作时,其耐磨性优于轴承钢,比青铜的耐磨性高几倍。在尼龙中添加聚四氟乙烯、二硫化钼、石墨或云母等固体润滑剂后,可降低摩擦系数;添加金属粉可增加导热性,而添加玻璃纤维等,也提高强度,增加耐磨性。
尼龙除整体使用外,还可作为表面耐磨涂层的涂料。
聚甲醛POM具有优良的综合性能,吸水性小,尺寸稳定,物理和机械性能超过尼龙。弹性模量和硬度高,在850℃以保持抗拉强度长期不变,耐腐蚀,摩擦系数低而稳定。但热稳定性差,收缩率大,在大气中曝晒易老化。
聚四氟乙烯聚四氟乙烯是一种结晶性高聚物,具有极优越的化学稳定性、热稳定性以及优越的电性能,PTFE形成的长链团分子中的碳原子被周围原子包围住,分子间的实际粘着力很小,形成低能量的表面,使表面分子可以相互滑动,呈现出极低的摩擦系数(0.1~0.04)。它与金属等摩擦时,能在极短时间内在金属表面上形成一层聚四氟乙烯转移膜,以致金属与PTFE的摩擦实际上成为PTFE对PTFE的摩擦。由于PTFE转移膜与金属形成强的化学键,故膜虽薄但也很牢固。
PTFE的缺点是耐磨性较差,机械强度低,受载后易变形,线膨胀系数大。因此PTFE作为减摩材料使用,主要是以填料形式添加到其他塑料中,或者在PTFE中添加金属或其他材料,以改善其机械性能、导热性和线膨胀系数。例如用碳素纤维增强的PTFE织物复合材料,其耐磨性和强度都可提高10倍。
芳纶盘根材料,以芳纶做主体材料,并浸渍了PTFE和高闪点的润滑材料,可在-100~60℃的条件下使用。芳纶又称聚芳酰胺纤维,由美国杜邦公司于1972年以“凯夫拉”(Kevlar)的商品名推出,其强度比钢高,比重只是钢的1/5,耐热性好。
膨胀聚四氟乙烯它是美国某公司在1969年为解决螺纹接头的密封问题而研制的,它将PTFE膨胀为一种高韧性和多孔性的低密度材料,将其应用在密封上获得了成功,取得了专利。EPTFE不仅保留了PTFE的化学稳定性好、摩擦系数低、不老化等性能,而且还扩大了使用温度范围,提高了机械强度、膨胀系数小、多孔性、正极高的韧性等。
成型工艺:分散PTFE树脂(润滑助剂)—混合—预成型糊膏—挤压—高速拉伸(低于PTFE熔点)—热定型(高于PTFE熔点温度下)—成品。
此外,用作减摩的聚合物材料尚有聚碳酸酯(PC)、聚矾(PSF)、聚酰亚胺(PI)等。