强度简介
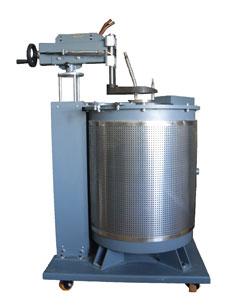
焦炭反应性
焦炭热强度是反应焦炭热态性能的一项机械强度指标(CSR%)。它表现焦炭在使用环境的温度和气氛下,同时经受热应力和机械力时,抵抗破碎和磨损的能力。焦炭的热强度有多种测定方法,
方法一
是热转鼓强度测定。测量焦炭的热转鼓强度,一般是将焦炭放在有惰性气氛的高温转鼓中,以一定转速旋转一定转数后,测定大于或小于某一筛级的焦炭所占的百分率,以此表示焦炭热强度。方法二
是称取一定200g焦炭试样,置于高温反应器中,把高温反应器置于焦炭反应性测定仪中,按启动键设备开始按程序升温,等温度升到1100±5℃时与二氧化碳反应2小时后,以焦炭质量损失的百分数表示焦炭反应性(CRI%)。高温反应后的焦炭经I型转鼓试验后,大于lOmm粒级焦炭占反应后焦炭的质量百分数,表示反应后强度(CSR%)。 (最新国标执行方法是方法二,标定设备:PL-500F焦炭反应性测定仪)
焦炭反应性是指焦炭与二氧化碳、氧和水蒸气等进行化学反应的能力。焦炭反应后强度是指反应后的焦炭在机械力和热应力作用下抵抗碎裂和磨损的能力。焦炭在高炉炼铁、铸造化铁和固定床气化过程中,都要与二氧化碳、氧和水蒸气发生化学反应。由于焦与氧和水蒸气的反应有与二氧化碳间的反应相类似的规律,因此大多数国家都用焦炭与二氧化碳的反应特性评定焦炭反应性(CSR%)。
中国标准GB/T4000-2008规定了焦炭反应性及反应后强度试验方法。其做法是使焦炭在1100±5℃高温下与二氧化碳发生反应,然后测定反应后焦炭失重率及其机械强度。
参考质料标准
GB/T4000-2008<<焦炭反应性及反应后强度试验方法>>
GB1997-89<<焦炭试样的采取和制备>>
GB/T2006-94<<冶金焦炭机械强度的测定方法>>
计算公式
焦炭反应性指标以损失的焦炭质量与反应前焦样总质量的百分数表示。焦炭反应性按下式计算:
CRI=(m-m1)/m×100%
式中:CRI-焦炭反应性,%
m-焦炭试样质量,g
m1-反应后残余焦炭质量,g。
焦炭反应后强度指标以转鼓后大于10mm粒级焦炭占反应后残余焦炭的质量百分数表示。反应后强度按下式计算:
CSR=m2/m1×100%
式中:CSR-反应后强度,%
m2-转鼓后大于10mm粒级焦炭质量,g
m1-反应后残余焦炭质量,g。
焦炭反应性CRI及反应后强度CSR的重复性,不得超过下列数值:
CRI:r≤2.4%
CSR:r≤3.2%
焦炭反应性及反应后强度的试验结果均取
平行试验结果的算术平均值。
焦炭反应性与二氧化碳、氧和水蒸气等进行化学反应的能力,焦炭反应后强度是指反应后的焦炭再机械力和热应力作用下抵抗碎裂和磨损的能力。焦炭在高炉炼铁、铸造化铁和固定床气化过程中,都要与二氧化碳、氧和水蒸气发生化学反应。由于焦与氧和水蒸气的反应有与二氧化碳的反应类似的规律,因此大多数国家都用焦炭与二氧化碳间的反应特性评定焦炭反应性。
中国标准(GB/T4000-1996)规定了焦炭反应性及反应后强度试验方法。其做法是使焦炭在高温下与二氧化碳发生反应没,然后测定反应后焦炭失重率及其机械强度。焦炭反应性CRI及反应后强度CSR的重复性r不得超过下列数值:
CRIr≤2.4
CSR:≤3.2
焦炭反应性及反应后强度的试验结果均取平行试验结果的算术平均值
指标标准
一级
冶金焦灰分A≦12.0;硫分S≦0.6%;抗碎强度M25≧92.0(M40≧80.0);耐磨强度M10 M25时,≦7.0 M40时,≦7.50;反应后强度CSR/%≧55;水分含量4.0±1.0二级冶金焦
灰分A≦13.5;硫分S≦0.8%;抗碎强度M25≧88.0(M40≧76.0);耐磨强度M10≦8.50;反应后强度CSR/%≧50;水分含量5.0±2.0三级冶金焦
灰分A≦15.0;硫分S≦1.0%;抗碎强度M25≧83.0(M40≧72.0);耐磨强度M10≦10.50;反应后强度CSR/%≧;水分含量≦12.0准一级冶金焦
灰分A﹤12.5%固定碳是焦炭的主要成分。将焦炭再次隔绝空气加热到850℃以上, 从中析出挥发物,剩余部分系固定碳和灰分。挥发分含量是焦炭成熟度的重要标志,挥发分含量过高表示焦炭不成熟(生焦),挥发分含量过低表示焦炭过烧(过火焦).生焦耐磨性差,使高炉透气性不好,并能引起挂料,增加吹损,破坏高炉操作制度。过火焦易碎,容易落入熔渣中,造成排渣困难,风口烧坏等现象.
转鼓强度
焦炭转鼓
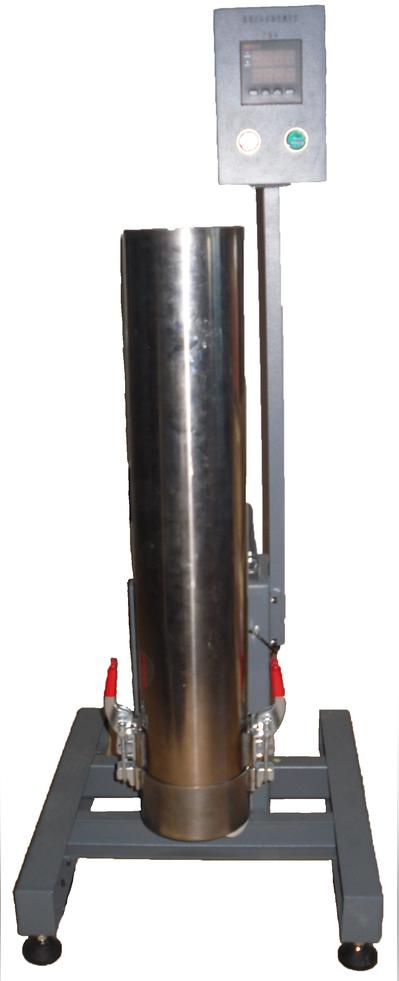
焦炭反应性
强度是表征常温下焦炭的抗碎能力和耐磨能力的重要指标,作转鼓强度试验时,将焦炭置于转动的鼓内,借助提升板反复地提起、落下。在此过程中,焦炭与鼓壁以及焦炭与焦炭相互撞击和摩擦,导致焦炭沿裂纹断开、表面磨损、粒度变小。焦炭强度即指焦炭经转鼓试验后,用大小两个粒级的焦炭量各占入鼓焦炭量的百分率分别表示的抗碎能力和耐磨能力。转鼓强度是在经验基础上,通过规范性的转鼓试验方法获得的一种块焦强度指标。参数简介
只需要一键操作,就能完成整个实验过程的操作系统!
产品特点:
国内首创气体流量全自动控制;独家控制仪整机采用电路气路集成一体化式设计,
焦炭反应性及反应后强度测试仪在符合GB/T4000-2008标准的同时,又在国内首创气体流量全自动控制系统。
一、国内首创气体流量全自动控制
1、
技术特点:对实验过程中CO2气的预热及CO2与N2气的切换实现了自动控制,计算机会根据控制的目标自动处理这些动作。
CO2与N2气自动控制,保证了实验数据结果更准确,可设定气体流量,系统会自动检测气体流量并进行调节。
流量控制系统的硬件采用了国际及国内知名品牌,以保证本产品的高度可靠性。气体切换采用电磁阀。
独家控制仪整机采用电路气路集成一体化式设计,使系统结构形式清晰简明,基本实现本控制仪的免维护。
2、流量控制技术指标:
▲ 最大流量:5L/min【CO2】;2L/min【N2】
▲ 准确度:±2%FS;
线性:±0.5%FS;
耐压:3MPa
▲气体管路连接:耐压:1MPa
输气管:进口高强塑管;
气体管路接头:可快速接插;
二、
控制系统特点1、技术特点:
使温度控制误差小于国家标准。
采用模糊PID温度控制算法,能有效预防外界干扰因素,使温度控制全程具有极好的稳定性能。
2、技术指标:
⒈额定温度: 1100℃
⒉控温范围:室温~1500℃
⒊温度分辨率: 1℃
⒋控温仪表精度等级:0.5级
⒌控温热电偶型号:铂铑10-铂(S型)2支
⒍加热炉电源电压: AC220/380V±10% 50Hz
⒎加热炉工作电流: 30A(可调)
⒏加热炉功率: 7~8KW
⒐升降电机电源电压:AC220/380V±10% 50Hz
⒑升降电机功率: 0.2KW
⒒电炉丝材料:高温合金电阻丝φ2.8mm~φ3.0mm
⒓试验用焦炭反应器:耐高温合金钢(GH44)
⒔时间设置:操作面板可设置开炉时间,24小时循环工作,
14.I型小转鼓:电源电压:AC220/380V
电机功率:0.2KW
三、
控制软件系统1、所有操作均在计算机界面上完成,不需要进行现场硬件的操作。
2、每次实验数据均以历史记录形式保存,历史记录可查。
3、实验过程中根据温度及工艺特性,系统会自动给出提示(包括声音及屏幕画面),同时会自动处理相关的每个 下一步的操作,一般情况下并不需要人为干预。
4、动态模拟显示界面,亲切友好。具有全软件操作能力,同时也保留了传统手动控制的方式(一般极少用)。
5、采用专用的工业界知名的组态软件,使系统稳定的运行得到有力保证。
抗碱性介绍
焦炭抗碱性是指焦炭在高炉冶炼过程中抵抗碱金属及其盐类作用的能力。焦炭本身的钾。钠等碱金属含量很低,约0.1%~0.3%,但是在高炉冶炼过程中,由矿石带入的大量钾和钠。在高炉内形成液滴或蒸气。造成碱的循环。并富集在焦炭中。使炉内焦炭的钾。钠含量远比入炉焦为高。可高达3%以上。这就足以对焦炭产生有害影响。在高碱负荷的高炉中,这种影响更为严重,因此抗碱性是对高炉焦的一个特殊要求。
钾、钠对焦炭反应性、焦炭机械强度和焦炭结构均会产生有害的影响,以致危害高炉操作。
(1)对焦炭反应性的影响。钾、钠对焦炭与CO2反应有催化作用。一般情况下,钾、钠在焦炭中每增加0.%~0.5%,焦炭与CO2的反应速度约提高10%~15%,钾、钠还可降低焦炭与CO2反应的开始温度。含3%钾、钠的焦炭比含0.1%~0.3%钾、钠的焦炭的反应开始温度约降低50~100℃。
(2)对机械强度的影响,钾。钠及其氧化物能渗入焦炭的碳结构。形成石墨钾、石墨钠等层间化合物。使碳结构变形,开裂而导致焦炭机械强度下降。
(3)对焦炭结构的影响,焦炭与CO2反应过程中,钾、钠的催化作用使表面反应增强,因此焦炭气孔壁的减薄程度加剧,钾、钠还使焦炭光学组织中的各向异性组分反应率有较大的增加,
(4)对反应后强度的影响,钾、钠虽然对焦炭与CO2的反应起催化作用。但在同一反应程度下。强度并不因钾。钠的存在而下降更多。这是因为催化作用虽然增强了焦炭的表层反应。却减轻了焦炭的内部反应,但在相同的反应时间内。碱金属能使反应程度加深。导致块焦反应后强度明显下降。
(5)对高炉操作的不良影响,钾。钠对焦炭质量的影响也会给高炉生产带来不良后果,焦炭与CO2反应的开始温度降低。可导致高炉炼铁焦比升高’由于焦炭与CO2反应速度增加。焦炭在高炉中的降解失重加剧,机械强度和块度急剧下降。导致焦炭在高炉下部高温区过多粉化。影响高炉顺行’钾。钠蒸气在高炉上部与煤气中的CO2反应生成碳酸盐而析出,这些碱金属碳酸盐部分粘附在炉壁上,会侵蚀耐火材料,影响高炉寿命。
提高焦炭抗碱性的措施有以下几点,
(1)增加低挥发分煤在配合煤中的用量,降低焦炭反应性,提高开始反应温度,从根本上缓解焦炭强度在高炉内的过早恶化。
(2)提高炼焦装炉煤的散密度,使焦炭气孔壁厚度增加,从而提高抵抗CO2的侵蚀能力。提高焦炭反应后强度。
(3)在炼焦配合煤可添加一些CO2反应的抑制剂或在焦炭表面喷洒这种抑制剂。以降低钾。钠对CO2反应的催化作用,曾以SiO2和B2O3作为抑制剂。进行提高焦炭抗碱性试验,试验表明。添加0.5%的B2O3后。焦炭反应性可降低30%~50%。
(4)减少碱金属在高炉内的循环,可以降低焦炭中的钾钠富集量,降低高炉炉身上部温度可减缓焦炭在进入软融带前发生过多的碳溶反应。从而使焦炭能承受更剧烈的反应而不致使强度过早变差。
质量评价
1、焦炭中的硫分:硫是生铁冶炼的有害杂质之一,它使生铁质量降低。在炼钢生铁中硫含量大于0.07% 即为废品。由高炉炉料带入炉内的硫有11% 来自矿石;3.5% 来自石灰石;82.5% 来自焦炭,所以焦炭是炉料中硫的主要来源。焦炭硫分的高低直接影响到高炉炼铁生产。当焦炭硫分大于1.6%,硫份每增加0.1% ,焦炭使用量增加1.8%,石灰石加入量增加3.7%, 矿石加入量增加0.3% 高炉产量降低1.5—2.0%. 冶金焦的含硫量规定不大于1%,大中型高炉使用的冶金焦含硫量小于0.4—0.7% 。
2、焦炭中的磷分:炼铁用的冶金焦含磷量应在0.02—0.03% 以下。
3、焦炭中的灰分:焦炭的灰分对高炉冶炼的影响是十分显著的。焦炭灰分增加1%,焦炭用量增加2—2.5% 因此,焦炭灰分的降低是十分必要的。
4、焦炭中的挥发分:根据焦炭的挥发分含量可判断焦炭成熟度。如挥发分大于1.5%,则表示生焦;挥发分小于0.5—0.7%, 则表示过火,一般成熟的冶金焦挥发分为1%左右。
5、焦炭中的水分:水分波动会使焦炭计量不准,从而引起炉况波动。此外,焦炭水分提高会使M04偏高,M10偏低,给转鼓指标带来误差。
6、焦炭的筛分组成:在高炉冶炼中焦炭的粒度也是很重要的。我国过去对焦炭粒度要求为:对大焦炉(1300—2000 平方米)焦炭粒度大于40 毫米;中、小高炉焦炭粒度大于25 毫米。但目前一些钢厂的试验表明,焦炭粒度在40—25 毫米为好。大于80 毫米的焦炭要整粒,使其粒度范围变化不大。这样焦炭块度均一,空隙大,阻力小,炉况运行良好。