生产线踏台
简介汽车企业在对焊装生产线进行前期规划过程中,着重在焊装车间的平面布置、焊装生产线柔性化设计、焊装车间物流方案等方面进行规划。
踏台设计的一般标准总原则:安全、实用、易制作、易安装、便于工装维修。
1、高度
踏台高度的制定应符合人体工程学标准,即采取直立姿势工作面的高度应符合设备高/人体身高=6/11的标准。结合焊装生产线的实际情况,确定焊钳的最舒适操作高度为900±150mm。在规划踏台高度时,应结合3D 焊点高度数据来制定踏台高度,超出范围的应做出相应修改。
2、宽度
踏台宽度制定按照生产线焊钳型号来确定最小宽度,以焊钳型号最大的焊钳能自由翻转为基数加 200mm 确定最小宽度,即假设焊钳 X30-6045 在整条生产线型号最大,焊钳能满足摆放和自由翻转要求的最小间距为800mm,则踏台宽度为1000mm。最大宽度应依据厂房设计中生产线钢结构两梁之间的距离而定,踏台装配到位后生产线应介于两梁之间,避免占据物流通道。
3、长度
踏台长度一般来说和整体生产线长度一致,首尾两端适当加长布置以保证操作者的安全生产,且应预留工位器具、焊接设备和电控柜等辅助设施的空间。
4、台阶
踏台台阶是整个踏台设计中需要考虑最多的环节。如台阶宽度、高度、开口位置等等。如图1踏台台阶示意图所示:
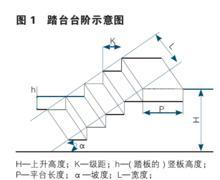
踏台
在踏台区域设置台阶时应考虑以下因素:①级距 K(两个相邻踏板之间的水平距离)和竖板高度 h(两个相邻踏板之间的垂直距离)应满足下式:600 ≤ K+2h ≤ 660。其中 h ≤ 250mm, K ≥ 100mm。结合现场实际经验和人机工程学理论,我们建议现场踏台设计中级距 K=230±30mm;竖板高度h=200±30mm。②坡度 α 应依据现场踏台高度、台阶最大宽度等因素来确定。一般情况下,α在30°~38°之间。③最上一级踏板应与梯段平台为同一水平面。④踏台楼梯的上升高度H一般不宜超过3m,在特殊情况下,这一高度也不应该超过 4m。否者,在连续到达另一梯段之前,需要增加一梯段平台,梯段平台的长度至少应为 800mm,并大于或等于梯段的宽度。⑤踏台开台阶的位置原则上应保证在相邻工位间设置一开口,依据现场工位器具、电控装置和焊接设备的分布情况而定。
5、护栏
为防止操作人员偶然跌落或偶然进入危险区域,需要在踏台区域装置护栏。一般在平台区域装配的平台护栏示意图如图 2 所示:
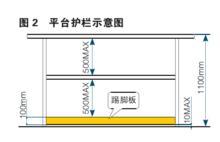
踏台
踏台区域增加平台护栏的原则:①当踏台高度超过 500mm 时,应安装护栏。②如果操作平台和机器构架或墙壁之间的间距小于 200mm 并且构架的防护等效于护栏时,不需要设护栏。但是,当操作平台和相邻的构架之间的间距大于 300mm 时,要有踢脚板。③护栏至少应包括一根中间横杆或某种其他等效防护。扶手和横杆及横杆与踢脚板之间的自由空间不应超过 500mm。④当用立杆代替横杆时,各立杆之间的水平间距最大为 180mm。⑤各支柱轴线间距离应限制在 1500mm 内。如果超过这一距离,应特别注意支柱的固定强度和固定的装置。⑥护栏高度一般设定为 1100mm。⑦增加护栏的具体位置应考虑生产工艺。如果踏台台阶过高、过窄或有其他特殊要求时,应在台阶处增加台阶护栏,保证生产安全。一般的台阶护栏示意图如图3所示:
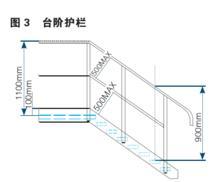
踏台
台阶护栏的制作要求是:①当台阶的上升高度超过500 mm并且斜梁外侧有大于 200 mm 的横向间距时,在其侧边应附加护栏。扶手的垂直高度至少应为 900mm。②为了保证安全抓握,扶手的直径应为25~50mm 之间的圆形截面或便于用手抓握的等效截面。③护栏至少应包括一根横杆或某一等效装置。扶手和横杆之间以及横杆和斜梁之间的净间距不应超过 500mm。④除安装固定支撑的下端面以外,在扶手长度方面上,扶手的100mm距离内没有障碍。6、踢脚板
踢脚板是为避免物体由地板平面下落而设置的护栏下部的实体零件,最小高度100mm的踢脚板应安置得离基面不大于10mm,踢脚板所有尖角应打磨成钝角。
7、其他
①使用的材料性能或经处理后(刷防锈漆)应能耐环境引起的腐蚀。②可能与使用者接触的某些部分应设计得不会产生伤害或阻滞(如避免尖角、焊接毛刺、粗糙的边缘等)。③各踏板和梯段平台应具有良好的防滑性能。④打开或关闭活动部分(门),应不会对使用者或附近的其他人产生进一步危险(例如剪切或偶然坠落)。⑤为了保证安全,装配用的附件、铰链、支座、支承件和安装件都应有足够的刚度和稳定性。⑥踏板和构架尺寸的设计应使它们能承受预期的载荷。⑦踏台平面之间的高度差应在 10mm 以下。
踏台设计和制造过程中的一些建议1、夹具、踏台一体化设计理念
许多企业的踏台制作理念是由负责焊装生产线规划的工艺规划师主控,按照前期积累的踏台设计经验及该生产线的规划需求,对现场踏台的高度、宽度和台阶位置等做一简单的数据分析,确定出踏台的具体尺寸进行制作。在夹具到达现场时,将前期制作踏台与现场夹具进行匹配并应用于生产。通过这个流程制作的踏台往往存在很大的问题,在实际生产过程中需要经过许多次的修改才能交付车间使用。这种方法既耽误生产进度,又存在安全隐患,造成资源的浪费。基于上述原因,建议将夹具、踏台进行一体化设计,将踏台的设计尺寸由夹具厂家主控。夹具厂家设计夹具的时候,对夹具的功能尺寸和配套设施(电控柜、电控开关、气路和电路)的分布有最直观的数据,并且当夹具制作完毕调试阶段,夹具厂家也能实际了解现场操作的要求,模拟现场情况的踏台设计更能满足今后生产的要求。这样做有几点好处:第一、更安全、相容性更好;夹具厂家在设计踏台时,踏台和夹具之间的间隙可通过多种方式进行控制,使踏台与夹具的接触曲面更贴合,相容性更好,实现踏台与夹具的“无缝结合”,消除了安全隐患。第二、节约成本;在公司工艺人员的配合下,由夹具厂家主控的踏台设计,踏台的一次成型率更高,可以避免后期的反复修改所带来的资源浪费。第三、便于维修;由于是夹具厂家主控踏台的设计,其势必将夹具前期的安装和后期的维修考虑到踏台的设计过程中来,这样更能大大避免踏台后期的修改和便利于后期的生产。
2、夹具前期规划建议
①建议夹具厂家在设计夹具时,将所有气路尽量安装在 BASE板以下,方便踏台匹配,避免踏台与夹具匹配时产生缝隙。②由于踏台只是生产过程中的配套设备,如果前期能将夹具做低或者将夹具置于地沟中,避免现场踏台的制作,既安全,又节约成本。③在前期规划时,将车间物流、电控柜放置、操作台布局、工位器具放置等生产线其他匹配设备考虑到规划中去。
3、踏台后期安装问题
①踢脚板制作和装配过程中,应避免产生直角。②踏台与夹具线匹配时避免产生缝隙。③所有方向朝外的踏台应使用蒙板包裹至踏台低端(距地面 10mm),更安全、更美观、更卫生。④踏台结构必须符合标准,并且踏台的角座需要加固,保证踏台的稳定性和平度。
基础应用
焊装调整线存在的问题操作者在焊装调整线上对驾驶室白车身总成进行的补焊、打磨、修磨和装调等,对驾驶室白车身总成质量具有举足轻重的作用。集瑞联合重工有限公司的焊装调整线由于工位较多、白车身尺寸较大,因此选择了滑橇输送式的线体结构。该焊装调整线主要由滑橇、驱动滚床(又称辊床)和电气控制系统(主要由PLC组成)等部分组成。载货汽车驾驶室白车身总成的高度尺寸远大于轿车白车身总成的高度尺寸,因此在焊装调整线两侧配备了高度为80~100cm的踏台,目的是方便
操作者对卡车白车身腰线以上部分进行相应操作。从实际使用情况看,这种踏台虽然能够为操作者在车身X向和Z向的操作提供很大的便利,但由于卡车白车身宽度尺寸较大,Y向操作仍存在操作盲区,相应钣金缺陷无法处理,如果勉强操作则存在安全隐患。
改进措施为解决上述问题,在现有操作台的基础上增加了伸缩式踏台工装,并需保证伸缩式踏台和白车身滑橇各自运行的安全性。
1、伸缩式踏台的驱动方式
目前常用的驱动方式有电动、液压传动和气动。前两种驱动方式需要较大的空间,气动驱动方式需要的空间相对较小,且所需气源是焊装调整线原来就具备的条件,因此伸缩式踏台采用气动驱动方式。
2、伸缩式踏台操作安全性的保证
焊装调整线滑橇式输送结构通过PLC技术根据编辑信号控制滑橇在滚床上的前进和停止等动作,伸缩式踏台也采用PLC技术控制踏台的伸出和缩回。滑橇式输送结构和伸缩式踏台都采用PLC控制技术可以使两者的信号进行互锁编辑,从而保证滚床和滑橇在运动时,伸缩式踏台无法工作,反之亦然,确保了操作的安全性。
3、伸缩式踏台的安装
伸缩式踏台的滚轮和导轨使用螺栓连接,通过对螺栓的上、下调节可以对滚轮和导轨进行上、下调节,从而保证踏台滚轮和导轨之间充分配合,也避免了由于地面的开裂或沉降等因素对伸缩式踏台运行的影响。