基本介绍
转向节通过三个衬套和两个螺栓与车身相连,并通过法兰盘的制动器安装孔与制动系统相连。在车辆高速行驶时,路面通过轮胎传递到转向节上的振动,是我们分析时考虑的主要因素。计算时利用已有的整车模型,对整车施加4G的重力加速度,算出转向节三个衬套中心点和两个螺栓安装孔中心点的支反力作为施加载荷,并约束法兰盘连接制动系统端面上所有结点的123456自由度。
应用范围
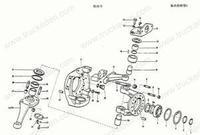
转向节
转向传动轴在汽车上应用比较广泛。在发动机前置后轮或全轮驱动的汽车上,由于弹性悬架的变形,变速器或分动器输出轴与驱动桥输入轴的轴线相对位置经常变化,所以普遍采用十字轴转向传动轴。在转向驱动桥中,内、外半轴之间的夹角随行驶需要而变,这时多采用等速转向传动轴。当后驱动桥为独立悬架时,也必须采用转向传动轴。转向节按扭转方向是否有明显的弹性,可分为刚性转向节和挠性转向节。刚性转向节是靠零件的铰链式连接传递动力的,可分成不等速转向节(如十字轴式)、准等速转向节(如双联式、凸块式、三销轴式等)和等速转向节(如球叉式、球笼式等)。挠性转向节是靠弹性零件传递动力的,具有缓冲减振作用。
不等速转向节是指转向节连接的两轴夹角大于零时,输出轴和输入轴之间以变化的瞬时角速度比传递运动,但平均角速度比为1的转向节。准等速转向节是指在设计角度下工作时以等于1的瞬时角速度比传递运动,而在其它角度下工作时瞬时角速度比近似等于1的转向节。输出轴和输入轴以等于1的瞬时角速度比传递运动的转向节,称之为等速转向节。
组成特点
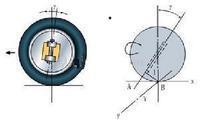
主销内倾角
转向节形状比较复杂,集中了轴、套、盘环、叉架等四类零件的结构特点,主要由支承轴颈、法兰盘、叉架三大部分组成。支承轴颈的结构形状为阶梯轴,其结构特点是由同轴的外圆柱面、圆锥面、螺纹面,以及与轴心线垂直的轴肩、过渡圆角和端面组成的回转体;法兰盘包括法兰面、均布的连接螺栓通孔和转向限位的螺纹孔;叉架是由转向节的上、下耳和法兰面构成叉架形体的定位参数
为了保持汽车直线行驶的稳定性、转向的轻便性和减小轮胎与机件间的磨损,转向轮、转向节和前轴三者之间与车架必须保持一定的相对位置,这种具有一定相对位置的安装称为转向轮定位,也称前轮定位。正确的前轮定位应做到:可使汽车直线行驶稳定而不摆动;转向时转向盘上的作用力不大;转向后转向盘具有自动回正作用;轮胎与地面间不打滑以减少油耗,延长轮胎使用寿命。前轮定位包括主销后倾、主销内倾、前轮外倾及前轮前束。
主销后倾角
主销后倾角
主销在汽车的纵向平面内,其上部有向后的一个倾角γ,即主销和地面垂直线在汽车纵向平面内的夹角,如图所示。主销后倾角γ能形成回正的稳定力矩,当主销具有后倾角γ时,主销轴线和路面的交点将位于车轮与路面接触点的前面。当汽车直线行驶时,若转向轮偶然受到外力作用而稍有偏转(向右偏转如图箭头所示),将使汽车行驶方向向右偏离。这时,由于汽车本身离心力的作用,在车轮与路面接触点b处,路面对车轮作用着一个侧向反力
。反力对车轮形成一个绕主销轴线作用的力矩L,其方向正好与车轮偏转方向相反。在此力矩的作用下,将使车轮回到原来的中间位置,从而保证汽车稳定直线行驶,故此力矩称为回正力矩。
但此力矩也不宜过大,否则在转向时为了克服该稳定力矩,驾驶员要在转向盘上施加较大的力(即所谓的转向沉重)。因稳定力矩的大小取决于力臂L的大小,而力臂L的大小取决于后倾角γ的大小。
现在一般采用的γ角不超过2-3°。现代高速汽车由于轮胎气压降低、弹性增加,而引起稳定力矩增大。因此,γ角可以减小到接近于零,甚至为负值。
主销内倾角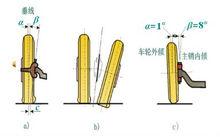
主销内倾角和车轮外倾角
主销在汽车的横向平面内,其上部向内倾斜一个β角(即主销轴线与地面垂直线在汽车横向平面内的夹角)成为主销内倾角。主销内倾角β也有使车轮自动回正的作用,如图所示。当转向轮在外力作用下由中间位置偏转一个角度时,车轮的最低点将陷入路面以下。但实际上车轮下边缘不可能陷入硬路面以下,而是将转向轮连同整个汽车前部向上抬起一个相应的角度。这样,汽车本身的重力有使转向轮回到原来中间位置的效应。
此外,主销的内倾还使得主销轴线与路面交点到车轮中心平面与地面交线距离c减小,从而可减小转向时驾驶员加在转向盘的力,使转向操纵轻便,同时也可以减小从转向轮传到转向盘的冲击力。但c值也不宜过小,即内倾角不宜过大,否则在转向时车轮绕主销偏转的过程中,轮胎与路面间将产生较大的滑动,因而增加了轮胎与路面间的摩擦阻力。这不仅是转向变得沉重,而且加速了轮胎的磨损。因此,一般内倾角β不大于8°,距离c一般为40-60mm。
主销内倾角是在前梁设计中保证的,由机械加工来实现。加工时,将前梁两端主销孔轴线上端向内倾斜就形成内倾角β。
车轮外倾角除上述主销后倾角和内倾角两个角度保证汽车稳定直线行驶外,车轮外倾角α也具有定位作用。α是通过前轮中心的汽车横向平面与前轮平面的交线与地面垂线之间的夹角,如图4(a)、(c)所示。如果空车时前轮的安装正好垂直于路面,则满载时,车桥将因承载变形而可能出现前轮内倾,这将加速轮胎的偏磨损。另外,路面对前轮的垂直反作用力沿轮毂的轴线分力,将使轮毂压向外端的小轴承,加重了外端小轴承及轮毂紧固螺母的负荷,安装前轮时应预先使其有一定的外倾角,以防止前轮内倾。同时,前轮有了外倾角也可以与拱形路面相适应。但是,外倾角也不宜过大,否则也会使轮胎产生偏磨损。
前轮的外倾是在转向节设计中确定的。设计时使转向节轴颈的轴线与水平面成一角度,该角度即为前轮外倾角α(一般为1°左右)。
前轮前束前轮有了外倾角后,在滚动时就类似于滚锥,从而导致前轮向外滚开。由于转向横拉杆和车桥的约束使前轮不可能向外滚开,前轮将在地面上出现边滚边滑的现象,从而加剧轮胎磨损。为了消除前轮外倾带来的这种不良后果,在安装前轮时,使汽车两前轮的中心面不平行,两轮前边缘间的距离B小于后边缘间的距离A,A-B之差成为前轮前束。这样可使前轮在每一顺势滚动方向接近于向着正前方,从而很大程度上减轻和消除了由于前轮外倾而产生的不良后果。
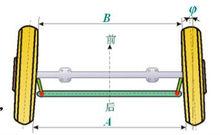
前轮前束
前轮前束可通过改变横拉杆的长度来调整。调整时,可根据各厂家规定的测量位置,使两轮前后距离差A-B符合规定的前束值。一般前束值为0~12mm。测量位置除了如图5所示位置外,还通常取两轮胎中心平面处的前后差值,也可以取两前轮轮辋内侧面处前后的差值。此外,前束也可用前束角表示。加工工艺
1.转向节是汽车重要安全零部件,全世界的行业人士都及其重视其安全特性,充分认识其安全特性对转向节的加工有着特别重要的作用,并应贯穿到整个制造过程的控制。
2.转向节分类,分体式主要用于乘用车(轿车),整体式主要用于商用车(货车);整体式又分为独立悬挂转向节和非独立悬挂转向节。从毛坯角度讲,整体式的锻造毛坯都属于比较有技术复杂系数的产品,对于机加,非独立悬挂转向节的加工比较有典型意义,下面所阐述的主要内容就是以非独立悬挂转向节作为标本来分析,起到触类旁通的作用。
3.转向节的加工分为毛坯制造和成品机加。目前,毛坯主要以锻件为主,也有采用铸造毛坯的,但比较少。毛坯的锻造工艺主要为劈叉、拔杆、预锻、终锻等工序组成,一般的锻造手册都可以查阅到这种典型工艺,国内的毛坯厂家比较多,网上可查。
4.下面说下机加:
从机加工艺来讲,转向节分为杆部、法兰盘和叉部等3个部分加工。
(1)杆部加工以中心孔定位,车和磨为主,加工关键是磨削。
(2)法兰盘加工主要是制动器安装孔的加工,要保证其位置度,同时要兼顾加工效率。并且,利用其中1孔作为加工叉部定位用。
(3)叉部加工是转向节加工的难点,采用两销一面定位,其加工主要是保证主销孔的同轴度,以及主销孔与内端面的垂直度,是整个加工工艺的投资重点和设备选型的关键。大部分转向节在此部位还有横拉杆装配用的锥孔,这更增加了叉部加工难度,锥孔加工是许多厂家难以100%合格的项目,应予重视,否则,转向节的早期失效就从这里开始。
(4)杆部的强化处理以提高转向节的疲劳寿命,对大多数类型的转向节都有这方面的技术要求,一般为滚压和中频淬火,以消除表面形成残余压应力,提高产品疲劳强度。国内加工对滚压要求不高,难点在中频淬火,主要是感应器的设计和制造,不过,在这方面国内有专业厂家给与解决。
(5)主销孔压装衬套后的加工,有的压装后不要求加工,有的压装后要求加工。从装配角度讲,压装后加工更有利于装配,否则影响转向的灵活性。
好了,以上就是转向节加工主要内容,根据具体转向节的不同,会有不同程度的变化,同时,加工设备的选择对整个工艺的影响比较大,因此,具体工艺应根据生产纲领和可供选择的设备来制订。
淬火处理
淬火是使钢强化的基本手段之一,将钢淬火成马氏体,随后回火以提高韧性,是使钢获得高综合机械性能的传统方法。
转向节的工作能力一般取决于强度和刚度,转向节经过淬火,使转向节的刚度强度都提高了,从而更加耐用,质量更高
常用转向节淬火设备有以下几种
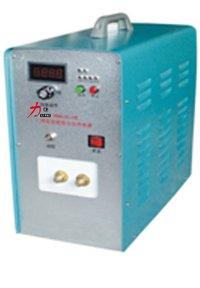
超音频淬火设备
16kw超音频淬火设备技术参数:型 号 | WH-VI-16 | 输入功率 | 16kw |
电 源 | 单相220V | 电 压 | 180-250V |
冷却水压 | 0.1Mpa | 输入电流 | 42A |
水温保护 | 55℃ | 效率 | 90% |
振荡频率 | 10-80KHz | 冷却水压 | 0.1Mpa |
外形尺寸 | 500×240×450 mm³ | 重量 | 20kg±5% |
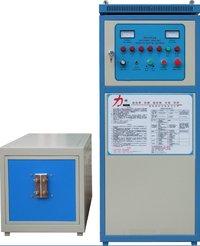
高频淬火设备
60Kw高频淬火设备技术参数:型号 | WH-VI-60 | 输入功率 | 60KW |
输入电压 | 342V-430V | 最大输入电流 | 90A |
冷却水流量(主机) | 25L/min(0.1mpa) | 冷却水流量(变压器) | 18L/min (0.1mpa) |
振荡频率 | 15-35KHZ | 冷却水压 | 0.1-0.3Mpa |
主机体积 | 590×450×780mm3 | 变压器体积 | 420×355×450mm3 |
主机重量 | 65±5%kg | 变压器重量 | 50±5%kg |
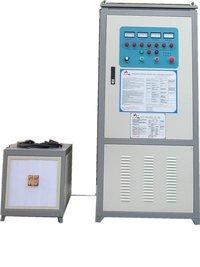
中频淬火设备
200kw中频淬火设备技术参数:型号 | GS-ZP-200 | 输入功率 | 200KW |
最大输入电流 | 300A | 工作电压 | 342-430V |
振荡频率 | 2-4KHz | 进水口水压 | 0.2-0.5Mpa |
主机体积 | 810*530*1780 | 分机体积 | 500*800*580 |
水温保护点 | 50℃ | 机身颜色 | 灰色+白色 |
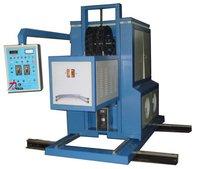
淬火机床
淬火机床技术参数:最大淬火长度 (mm) | 4000 | 最大回转直径 ( mm) | ≤φ500 |
工件移动速度 ( mm/s) | 2-60 | 旋转速度 (r/min) | 25-125 |
顶尖移动速度 ( mm/min) | 480 | 工件重量 ( kg) | ≤1500 |
输入电压 ( V ) | 三相380 | 电机总功率 ( kw) | 3 |
技术突破
在2008~2010年期间爆发的全球金融危机将整个汽车行业拖入了一个前所未有的低谷。经过此次危机后,随着行业逐渐回暖,在旺盛需求的推动下汽车厂商们正想方设法缩短交货期。现在,数以百万计的零配件必须要在很短的时间内加工完成,所以如何提高生产效率已成为应对该行业挑战的关键所在。
最近,伊斯卡推出了一系列解决方案,可有效避免停机时间,缩短零件加工周期,削减单件加工成本(CPP),由此提高生产效率。这些高效加工方案的突出优势还包括:革命性3P(高性能、高生产率、高收益率)理念、束魔涂层技术(SUMO TEC)硬质合金牌号及涂层、工程方面以及创新性研发。伊斯卡决定将汽车配件划分为多个门类(应用)并针对性地制定系统性的优化加工解决方案。转向节便属于其中的一种应用。
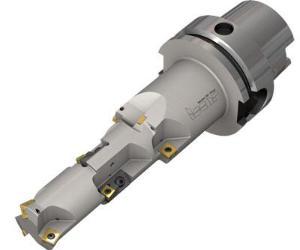
粗镗和精镗后,锪孔和倒角。所有操作由一
转向节是最复杂最精密的汽车零配件之一。要实现快速低成本生产,采用高效的精密切削刀具不可或缺。以往转向节都是由铸铁或钢材制成的,但目前市场趋向于改用铝合金。一方面,这是出于减轻汽车重量,提高燃油经济性的优化需要。另一方面,采用铝合金的加工成本要远远低于采用铸铁的加工成本(分别为15~25美分和约1美元)。不过,并非所有情况下,铝合金转向节都可以替换铸铁或钢质转向节,但不论何种时候(铝合金或铸铁),都可以通过以下方法来降低加工成本:采用组合刀具、采用FMR(快速金属切削)刀具和采用换刀速度快的刀具。采用组合刀具
采用组合刀具,避免换刀是最省钱的办法之一。而且,由于许多转向节加工用的数控机床刀库容量往往有限,采用组合刀具有时不仅仅是建议,也是必要的措施。
采用FMR(快速金属切削)刀具
采用FMR(快速金属切削)刀具可以缩短加工时间并节省额外成本。
1.更高的进给量
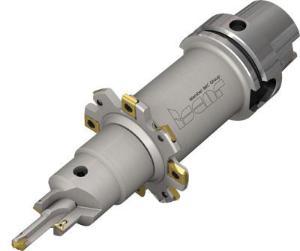
槽铣刀,前端带钻头及锪孔
伊斯卡束魔变色龙钻(SUMOCHAM)的进给量比常规硬质合金钻提高多达2倍。传统硬质合金钻受碳化钨(WC)的力学性质限制,无法承受相对较高的扭矩并容易损坏,只能采用很小的转进给量。这意味着制造商们无法充分“挤压”机床的性能,只能低效率工作。相比之下,束魔变色龙钻主体由高强度刀具钢制成,可以承受很高扭矩载荷。此外,和这种可换刀头设计理念相比,硬质合金钻还有一个弱点,对总体跳动较敏感,T.I.R.(总体指标偏差)容易造成硬质合金意外折断。相比钢制钻杆,硬质合金钻头钻杆承受弯曲变形的能力极其有限。只要总体跳动值比平均值稍微高出一点,它就很容易折伊斯卡束魔变色龙(SUMOCHAM)可换头式钻削系统拥有以下诸多优点,由此成为全球转向节制造商的首选:AlTiN涂层硬质合金刀头结合钢制钻杆,可提升端面钻削加工的每转进给量多达2倍;刀头更换,无需对刀时间;头多次更换也不会影响刀槽寿命;易于集成至柔性组合刀具,适合定制刀具设计。
2.更高的切削速度
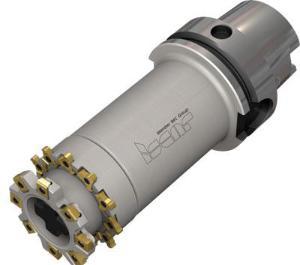
凹槽铣
例如,对于铝合金转向节:经PCD(聚晶金刚石)或DLC(类金刚石)涂层刀具的加工速度远超未经涂层的硬质合金。虽然这些刀具价格更贵,但由于切削快、寿命长,投资回收快且单件加工成本低很多。转向节一般都是大批量生产的,故PCD和DLC涂层刀具性价比极高,应用广泛。最要注意的问题是采用合适的冷却液并确保其以适当的角度喷向切削区域,从而提供有效的润滑并避免产生积屑瘤。3.全新刀具设计理念
采用全新刀具设计理念,大幅增加刀齿密度,从而成倍提高加工效率:转向节的主轴承孔采用镗杆、带导向块的单刃铰刀或可调式双刃镗刀进行精加工。
这些方法十分可靠,因此长期被人们应用。缺点是进给量超低(采用单刃或双刃刀具时进给速度只能保持0.15~0.3mm/r),延缓了整个加工过程。
为了加快加工速度,转向节制造商们试图用多齿钎焊铰刀替代这些传统刀具,这解决了加工周期过长的问题,但又产生了一个新的问题。大直径铰刀价格昂贵,如果每次磨损就要更换,用户很不划算。此外,由于主轴承孔公差要求极高,这些铰刀无法进行重磨。
后来,这一老办法有了新的改进。它是一种微调式铰刀环,带有钎焊硬质合金切削刃。这种刀具切削速度很快(例如用10齿铰刀环加工一个?90.0H6孔,其进给量可以达到1mm/r),并且可以使用一颗锥头螺钉进一步调整直径来补偿磨损。这种直径调整机制可以达到很高的公差,在大多数情况下有利于延长刀具的寿命。铰刀环很快成为了加工主轴承孔的常用刀具,但由于以下致命缺点,这一设计理念没能成为一种最彻底的解决方案:
如果某个刀刃产生了缺口(由于工件材料质量差等原因,这种情况时有发生),会暴露未涂层的基体而形成积屑瘤(BUE),导致精加工表面受损;无法均匀调整刀齿,因此无法精确控制径向偏差。因此,一些刀齿会参与比其他刀齿更深的切削,加速了其过度磨损。
刀齿磨损后,铰刀环需要送去重新安装刀齿。重新安装费用不菲,通常占到了新铰刀环价格的65%~70%。用户还必须控制铰刀环库存,以便安排重新修磨和重涂层等。所有这些都要占用额外的资源,所以许多用户都不喜欢这个办法。
那么转向节主轴承孔精加工的终极刀具在哪里呢?多年前,伊斯卡的研发专家们想出了一种新办法,并立刻赢得了汽车业的热烈追捧。
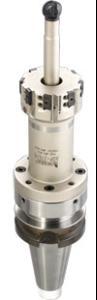
伊斯卡主轴承内孔精加工用铰孔系统搭配变
这种全新刀具是一种可换刀片式微调多齿铰刀。每一个刀片都可以在几秒钟内单独进行精密的调整以获得所需直径。凭借这些功能,这种铰刀既满足高孔径公差要求,又消除了铰刀的径向偏差问题,延长了刀具的寿命。此外,高强度的立装刀片,提高了加工经济性:具有4个切削刃。切削刃不需重新刃磨和重新涂层。多数情况下,转向节加工机床具有两个主轴,为此伊斯卡还提供第二套方案作为备用(一把为右手刀,备用的为左手刀),左手铰刀可以使用右手铰刀未使用的额外的4个切削刃,刀片性价比更高。可视情况轻松地更换刀片牌号(在钎焊铰刀上这是不允许的)。采用换刀速度快的刀具
采用不用从机床取出即可更换刀片或刀片更换速度超快的刀具,从而避免或缩短停机时间并节省额外费用。