设备简介
液力传动是液体传动的一个分支,它是由几个叶轮组成的一种非刚性连接的传动装置。这种装置把机械能转换为液体的动能,再将液体的动能转换为机械能,起着能量传递的作用。
值得注意的是,液力传动与液压传动是不同的,液力传动是依靠液体的动能来传递能量的,而液压传动则是依靠液体的压力能传递能量的。
设备特点
液力传动具有很多优点,但是也存在一些缺点,它主要有以下优点:
自动适应性
液力变矩器的输出力矩能够随着外负载的增大或减小而自动地增大或减小,转速能自动地相应降低或增高,在较大范围内能实现无级调速,这就是它的自动适应性。自动适应性可使车辆的变速器减少挡位数,简化操作,防止内燃机熄火,改善车辆的通用性能。液力耦合器具有自动变速的特点,但不能自动变矩。
防振隔振性能
因为各叶轮间的工作介质是液体,它们之间的连接是非刚性的,所以可吸收来自发动机和外界负载的冲击和振动,使机器启动平稳、加速均匀,延长零件寿命。
透穿性能
指泵轮转速不变的情况下,当负载变化时引起输入轴(即泵轮或发动机轴)力矩变化的程度。由于液力元件类型的不同而具有不同的透穿性,可根据工作机械的不同要求与发动机合理匹配,借以提高机械的动力和经济性能。
另外,还具有过载保护、自动协调、分配负载的功能。液力传动并不完美,它也是有缺点的,比如:效率较低、高效范围较窄,需要增设冷却补偿系统,使结构复杂、成本高。
基本原理
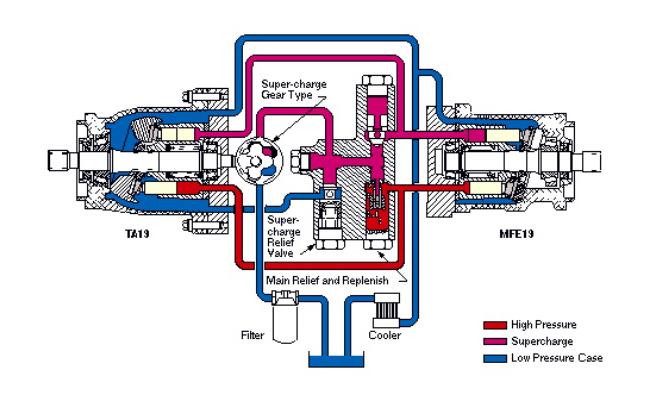
图1 液力传动原理图
液力传动的基本原理可以用下图来说明。原动机(内燃机、电动机等)带动泵轮旋转,使工作液体的速度和压力增加,这一过程实现了机械能向液体动能的转化;然后具有动能的工作液体再冲击涡轮,此时液体释放能量给涡轮,使涡轮转动将动力输出,实现能量传递。装置介绍
液力传动装置是以液体为工作介质以液体的动能来实现能量传递的装置,常见的有液力耦合器、液力变矩器和液力机械元件。
目前,液力传动元件主要有液力元件和液力机械两大类。液力元件有液力耦合器和液力变矩器;液力机械装置是液力传动装置与机械传动装置组合而成的,因此,它既具有液力传动变矩性能好的特点,又具有机械传动效率高的特征。
液力传动装置主要由三个关键部件组成,即泵轮、涡轮、导轮。
泵轮:能量输入部件,它能接受原动机传来的机械能并将其转换为液体的动能;
涡轮:能量输出部分,它将液体的动能转换为机械能而输出;
导轮:液体导流部件,它对流动的液体导向,使其根据一定的要求,按照一定的方向冲击泵轮的叶片。
液力耦合器
液力耦合器如下图所示,它是由泵轮和涡轮组成的。泵轮与主动轴相连,涡轮与从动轴相接。如果不计机械损失,则液力耦合器的输入力矩与输出力矩相等,而输入与输出轴转速不相等。因工作介质是液体,所以泵轮和涡轮之间属非刚性连接。
液力变矩器
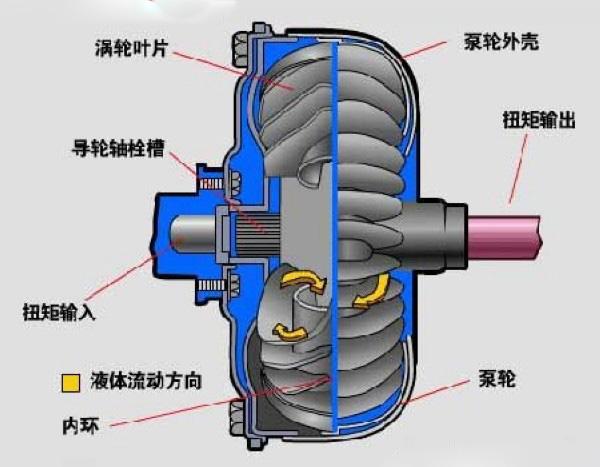
图3 液力变矩器
下图a是液力变矩器的实物模型图,图b是其结构原理简图。它主要由泵轮、涡轮、导轮等构成。泵轮、涡轮分别与主动轴、从动轴连接,导轮则与壳体固定在一起不能转动。当液力变矩器工作时,因导轮D对液体的作用,而使液力变矩器输入力矩与输出力矩不相等。当传动比小时,输出力矩大,输出转速低;反之,输出力矩小而转速高。它可以随着负载的变化自动增大或减小输出力矩与转速。因此,液力变矩器是一个无级力矩变换器。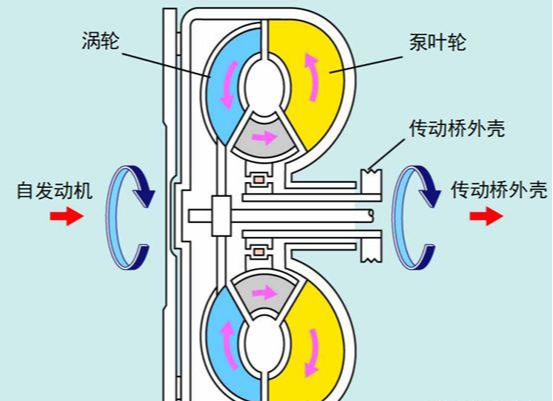
图4 三元件综合式液力变矩器
下面以目前广泛使用的三元件综合式液力变矩器来具体说明其工作原理。如图4所示,泵轮与变矩器外壳连为一体,是主动元件;涡轮通过花键与输出轴相连,是从动元件;导轮置于泵轮和涡轮之间,通过单向离合器及导轮轴套固定在变速器外壳上。
发动机启动后,曲轴通过飞轮带动泵轮旋转,因旋转产生的离心力使泵轮叶片间的工作液沿叶片从内缘向外缘甩出;这部分工作液既具有随泵轮一起转动的圆周向的分速度,又有冲向涡轮的轴向分速度。这些工作液冲击涡轮叶片,推动涡轮与泵轮同方向转动。
从涡轮流出工作液的速度可以看为工作液相对于涡轮叶片表面流出的切向速度与随涡轮一起转动的圆周速度的合成。当涡轮转速比较小时,从涡轮流出的工作液是向后的,工作液冲击导轮叶片的前面。因为导轮被单向离合器限定不能向后转动,所以导轮叶片将向后流动的工作液导向向前推动泵轮叶片,促进泵轮旋转,从而使作用于涡轮的转矩增大。
随着涡轮转速的增加,圆周速度变大,当切向速度与圆周速度的合速度开始指向导轮叶片的背面时,变矩器到达临界点。当涡轮转速进一步增加时,工作液将冲击导轮叶片的背面。因为单向离合器允许导轮与泵轮一同向前旋转,所以在工作液的带动下,导轮沿泵轮转动方向自由旋转,工作液顺利地回流到泵轮。当从涡轮流出的工作液正好与导轮叶片出口方向一致时,变矩器不产生增扭作用(这时液力变矩器的工况称为液力偶合工况)。
液力耦合器其实是一种非刚性联轴器,液力变矩器实质上是一种力矩变换器。它们所传递的功率大小与输入轴转速的3次方、与叶轮尺寸的5次方成正比。传动效率在额定工况附近较高:耦合器约为96~98.5%,变矩器约为85~92%。偏离额定工况时效率有较大的下降。根据使用场合的要求,液力传动可以是单独使用的液力变矩器或液力耦合器;也可以与齿轮变速器联合使用,或与具有功率分流的行星齿轮差速器(见行星齿轮传动)联合使用。与行星齿轮差速器联合组成的常称为液力-机械传动。
液力传动装置的整体性能跟它与原动机的匹配情况有关。若匹配不当便不能获得良好的传动性能。因此,应对总体动力性能和经济性能进行分析计算,在此基础上设计整个液力传动装置。为了构成一个完整的液力传动装置,还需要配备相应的供油、冷却和操作控制系统。
应用方面
液力传动用于现代化机器始于20世纪初,最早作为船舶动力装置与螺旋桨之间的传动机构,解决大功率、高转速的气轮机和转速受到“气蚀”限制的螺旋桨间的减速传动问题。20世纪30年代,瑞典的阿尔夫·里斯豪姆与英国里兰汽车公司的史密斯工程师合作研制了里斯豪姆一史密斯型三级液力变矩器,先后应用到公共汽车和其他车辆上。20世纪40年代,液力传动在军事装备上得到了较广泛的应用,如:打捞绞车、登陆艇的锚链绞车、坦克、自行火炮等,同时,带动了液力传动在汽车、拖拉机、工程机械等相关领域的应用和发展。现在液力传动已广泛应用于汽车、拖拉机、工程机械、建筑机械、铁路机车、坦克装甲车辆、石油钻探机械、起重运输机械、风机、水泵等产品上。
20世纪50年代末,我国开始自行设计制造液力传动,在高校、研究所和相关工厂的共同努力下,首先在轿车和内燃机车上得到了应用。经过50多年的发展,液力传动已在我国得到了广泛的推广和应用,现在,国内工程机械、起重运输机械、车辆等行业广泛采用液力传动装置。